BMC Compression Mold
Specializing in manufacturing composite BMC compression molds, precise customization,leading BMC mold innovation, providing unlimited possibilities for your projects,create the future together

What is BMC(Bulk Molding Compound) Compression Mold
BMC (Bulk Molding Compound) compression mold, also known as a BMC compression molding tool, is a specialized mold used in the manufacturing process of components made from Bulk Molding Compound (BMC). BMC is a type of thermosetting composite material that consists of a mixture of thermosetting resin, chopped glass fibers, mineral fillers, and various additives. It is commonly used in industries such as automotive, electrical, and appliance manufacturing for producing parts with high mechanical strength and dimensional stability.
BMC mold is a high-energy tool widely used in the plastic molding industry. Its unique design and advanced technology make the production process of plastic products easier and more efficient, while also improving product quality and reliability.
At present, BMC molds have been used in automobiles, energy, electrical appliances, catering services, household appliances, optical instrument components, industrial and construction supplies and other fields. WS Mold is engaged in the design and manufacturing of hot pressing molds for BMC composite molding molds, and has developed a variety of BMC mold products, such as fiberglass automotive parts, composite manhole covers, electrical boxes, meter boxes, etc.
WS (WINSEN) is a processing enterprise specializing in the production of BMC composite molds and products, providing customers with composite mold products and application solutions.
BMC materials have excellent physical and chemical properties, making them an excellent material for many composites products. The BMC mold is a tool specially used to process BMC parts.BMC molds are usually made of metal materials, such as steel. The cavity inside the mold is designed to match the shape of the final product. During the manufacturing process, BMC material is added to the mold, and then high pressure is applied through hot or cold pressing to fill the entire mold cavity. After a certain period of curing, the mold is opened and the molded BMC product can be obtained.
What is BMC Mold Forming Process
BMC (Bulk Molding Compound) mold is a tool used to manufacture BMC composite products. BMC molds are formed by compression molding. Compression molding is a method of shaping thermosetting materials by applying both intense pressure and elevated temperature to achieve the desired form.
The following is the process of BMC mold forming:
- Material Preparation: BMC material is prepared by mixing the various components to create a uniform compound.
- Material Compression: The prepared BMC material is placed into the mold cavity.
- Mold Closure: The BMC molds are typically made of steel, is closed to enclose the BMC material.
- Molding and Curing: The closed mold is subjected to both heat and pressure. The heat causes the thermosetting resin in the BMC material to cure and harden, while the pressure ensures the material takes on the mold’s shape.
- Cooling: After curing, the mold is cooled to solidify the part.
- Mold Opening: Once the part has fully cured and solidified, the mold is opened, and the finished component is removed.
As an advanced mold manufacturing technology, BMC mold is gradually becoming the precision choice in the industrial field.BMC is a thermoset plastic that is mixed with various inert fillers, fiber reinforcements, catalysts, stabilizers and pigments to form a sticky “putty-like” composite for compression or injection molding. BMC has many unique properties, such as high hardness, light weight, corrosion resistance, UV resistance, good insulation, excellent thermal properties, etc., which make BMC more satisfactory than thermoplastics.
The compression molding process uses the characteristics of each stage in the resin curing reaction to achieve product molding, that is, the molding material plasticizes, flows and fills the mold cavity, and the resin solidifies.

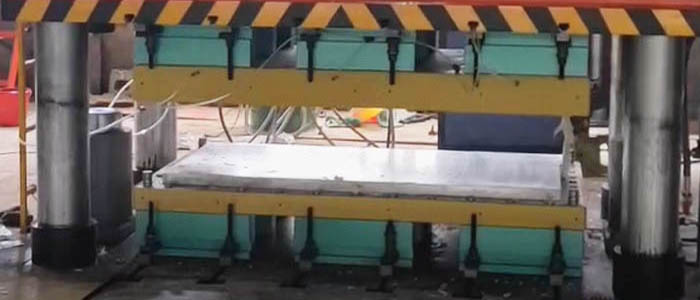
BMC molds are essential for producing components with complex geometries, high electrical insulation properties, and resistance to corrosion and heat. These molds are used for manufacturing various parts such as electrical insulators, automotive components, and appliance parts, where high-strength and dimensional stability are critical.


Advantages of BMC Compression Mold
Stable product quality
BMC molds have excellent precision and stability, ensuring that the size and shape of each plastic product are consistent, thereby reducing the defective rate.
High production efficiency
Compared with other molding methods, BMC molds have a short production cycle and high production efficiency. Once the mold design is completed, mass production can be carried out continuously through automated production lines to increase production capacity.
Complex structure molding
BMC molds can achieve high-precision molding of complex structures, which is difficult or impossible to achieve in other plastic molding methods.
Material saving
In the production process of BMC mold products, the material utilization rate is high and there is almost no waste, which is beneficial to reducing costs.
Environmental protection and energy saving
There is no need to heat plastic particles during the BMC mold molding process, thus saving energy. At the same time, the BMC material itself also has environmentally friendly properties.
As an important tool for the production of plastic products, BMC mold plays an irreplaceable role in the plastic molding industry. Its high energy efficiency, high precision and diverse molding capabilities make it popular in various fields. However, we must also recognize the importance of quality control and maintenance in the process of using BMC molds. Only by continuously optimizing the production process and improving the level of mold manufacturing can the BMC mold industry continue to prosper and develop in the future.
Application areas of BMC molds
BMC molds are widely used in various fields, such as electrical and electronics, transportation, architectural decoration, medical equipment, etc. Among them, some products with high requirements, such as cable terminals, auto parts, building exterior wall panels, etc., are usually produced using BMC molds.
Automotive industry
BMC molds are widely used in the manufacturing of automotive exterior and interior parts, such as lamp housings, door handles, instrument panels, etc.
Electronic and electrical
BMC molds can be used to manufacture electrical components such as insulators and circuit breaker housings to ensure safe and stable operation of electrical equipment.
Communication equipment
BMC molds are used to manufacture communication radomes, signal transmission modules, etc., to meet the high-frequency insulation performance requirements of communication equipment.
Construction field
BMC mold products play an important role in building exterior wall decoration, waterproof materials, etc.
Medical equipment
BMC molds are used in the manufacture of medical equipment, such as medical ultrasonic probes, X-ray machine casings, etc.



The significance of BMC molds to industrial development
As a high-performance composite material, BMC mold is of great significance in promoting industrial development.
Improve product quality: The precision molding capabilities and excellent performance of BMC molds have significantly improved product quality and met the stringent requirements of modern industry for product quality.
Promote lightweight development: BMC molds are lighter than traditional metal materials, which is beneficial to reducing product weight and promoting lightweight development.
Expand new application fields: The special properties of BMC molds enable it to be used in more fields, opening up new possibilities for the continuous advancement of industrial technology.
Promote green manufacturing: The environmentally friendly and energy-saving characteristics of BMC molds are conducive to promoting green manufacturing and reducing the impact on the environment.
As a high-performance, high-precision composite material, BMC mold is gradually leading the trend of industrial manufacturing. Its wide application in automobiles, electronics, communications, medical and other fields has brought a qualitative leap to all walks of life. With the continuous innovation of technology, I believe that BMC molds will play a more important role in future industrial development, shaping a more precise and high-energy industrial world.
BMC mold quality control and maintenance measures
As a high-energy tool in the field of plastic molding, BMC molds are widely used in various fields with their unique principles and advantages. With the continuous advancement of technology and changing market demands, I believe that BMC molds will continue to develop and grow, bringing more convenience and possibilities to the production of plastic products. 5. Quality control and maintenance of BMC molds
When using BMC molds for production, quality control and maintenance are particularly important. Only by keeping the mold in good condition can the stable quality of the product be ensured. The following are some key quality control and maintenance measures:
Mold design and manufacturing
The design of the mold must comply with the shape and size requirements of the product to avoid defects. In the mold manufacturing process, high-quality materials and advanced technology must be used to ensure the durability and accuracy of the mold.
Process parameter control
During the BMC mold production process, process parameters such as temperature, pressure, curing time, etc. must be strictly controlled. Reasonable process parameters can ensure product consistency and stability.
Mold maintenance
Regular maintenance of BMC molds is the key to ensuring long-term stable production. The mold surface must be kept clean to avoid affecting product quality. At the same time, check whether the mold is damaged or worn, and repair or replace it in time.
Mold storage and maintenance
When the BMC mold is not used temporarily, it should be properly stored and protected against moisture and dust to prevent damage to the mold.
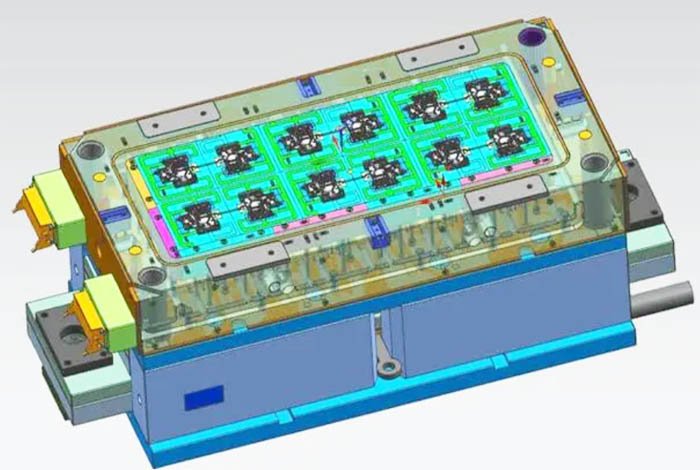

BMC Compression mold technology challenges
Although BMC molds have many advantages, their technological development also faces some challenges. These mainly include the following points:
Material research and development: The high-performance composite materials required for BMC molds need to be continuously developed and improved to meet the material performance needs of different industries. Material stability, cost control and sustainable development are difficult problems that need to be continuously overcome.
Manufacturing process: Compared with traditional molds, the manufacturing process of BMC molds is more complex and requires higher equipment and processes. Therefore, the improvement of the stability and cost-effectiveness of the manufacturing process is a direction that requires continuous optimization.
Market awareness: Compared with traditional materials and mold manufacturing technology, the market awareness of BMC molds in some fields is still relatively low. Promoting and popularizing the knowledge and advantages of BMC mold technology is crucial to accelerating its application and development.
Faced with these challenges, the development of BMC mold technology has not stopped. Scientific researchers and enterprises are actively investing in research and development, continuously improving the performance and manufacturing processes of BMC materials, and improving production efficiency and stability. At the same time, the increasing demand for high-performance materials and precision manufacturing in various industries has also provided a broader market space for BMC mold technology.


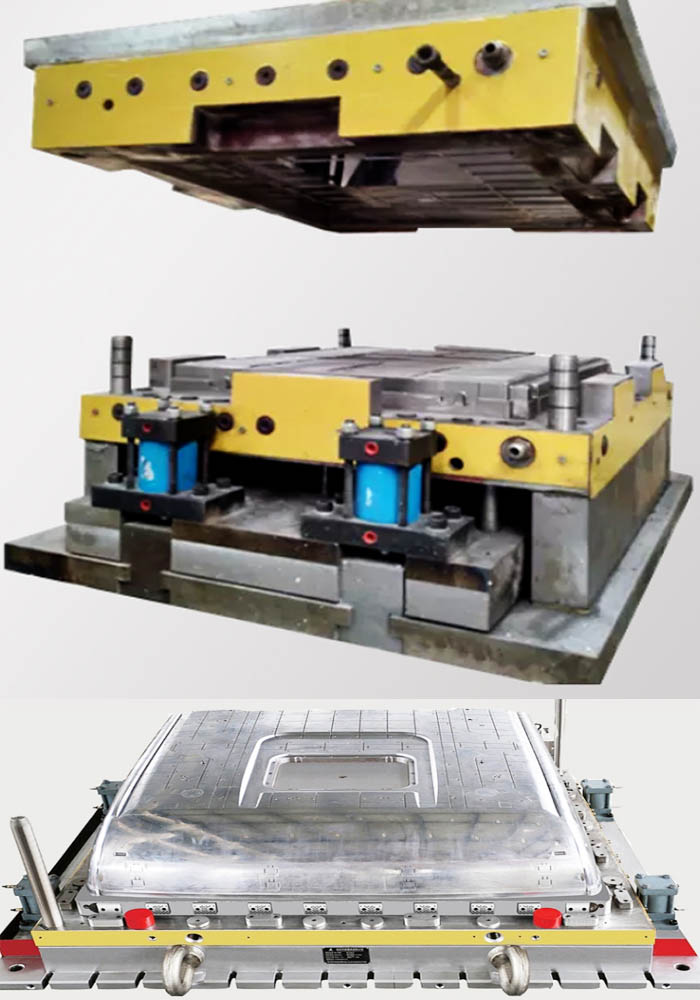
BMC Mold Future Outlook
With the rapid development of science and technology and the advancement of industrial technology, BMC molds will play a more important role in the future. From automobiles, electronics to aerospace, the demand for high-performance and precision manufacturing in various fields is increasing, and the excellent characteristics of BMC molds just meet these needs.
It is expected that BMC mold technology will make more breakthroughs in the following aspects in the future:
Application of new materials: With the development of new material technology, more high-performance resins, fibers and fillers will be used in BMC molds to further improve their performance.
Integration of intelligent manufacturing: With the promotion of Industry 4.0 and intelligent manufacturing concepts, BMC mold manufacturing will become more digital and automated, improving production efficiency and stability.
Expansion of emerging fields: BMC mold technology will continue to expand new application fields, such as new energy vehicles, biomedical equipment, etc., and promote the innovation and development of industrial technology.
In the future, the BMC mold industry is expected to usher in more opportunities. With the development of science and technology, the introduction of new technologies such as 3D printing technology and intelligent mold manufacturing will further improve the manufacturing level and production efficiency of BMC molds. At the same time, with the increasing awareness of environmental protection, BMC mold materials and manufacturing processes will also pay more attention to green environmental protection and achieve sustainable development.
As a high-performance, precision-manufactured composite material, BMC mold is gradually changing the pattern of industrial manufacturing. Its wide application in automobiles, electronics, medical and other fields has brought more possibilities to industry. Facing future development, we have a more optimistic outlook for BMC mold technology. It is believed that with the joint efforts of scientific researchers, manufacturing companies and all walks of life, BMC molds will continue to become the precise choice to shape the future industry and promote industrial technology to a higher level.
At present, the BMC mold industry is in a stage of rapid development. As the demand for plastic products increases, the need for high-energy, high-quality production becomes increasingly urgent. As a high-quality plastic molding tool, BMC mold has received widespread attention.