Insert Molding Molds & Part
Insert injection molding can be save savings
Structurally more stable!
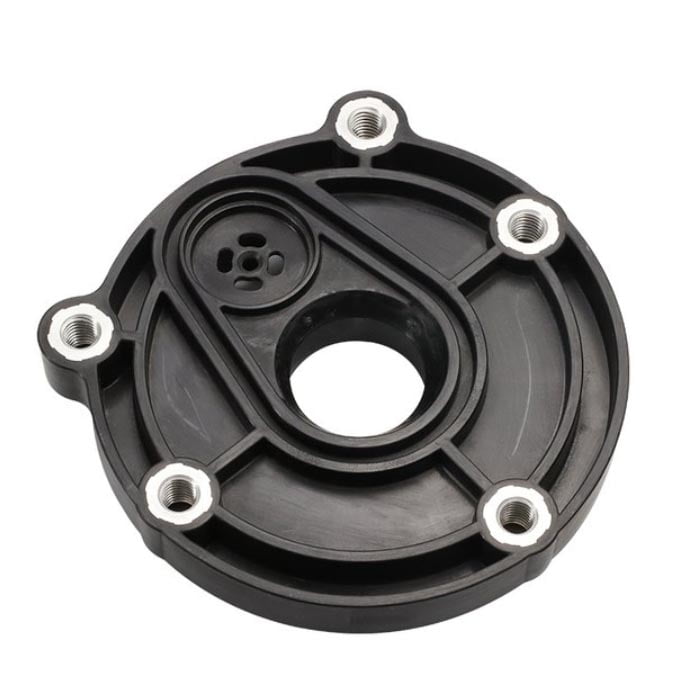
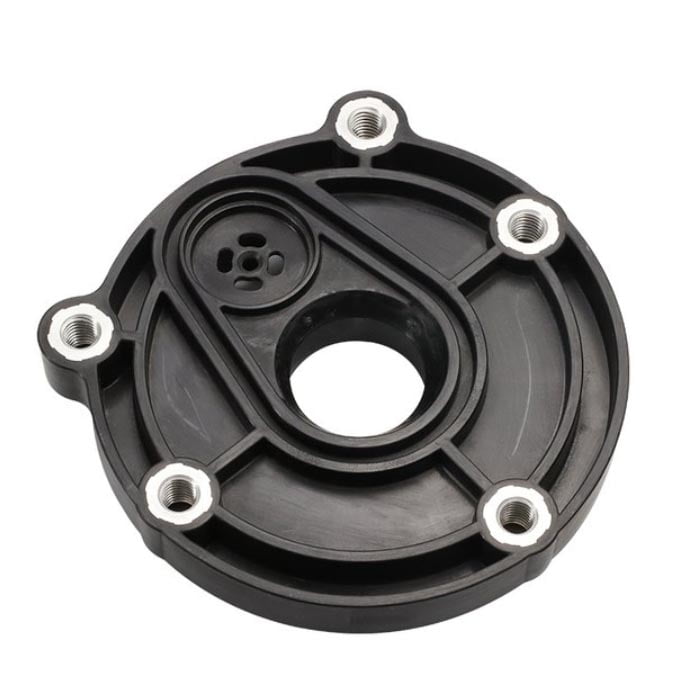
What is insert injection molding ?
Insert molding refers to a molding method in which pre-prepared inserts of different materials are placed into the mold, and then the molten material is injected and joined to the inserts, thereby producing an integrated product.
Inserts are often metal parts and are used to enhance the mechanical properties of plastic parts. Insert molding eliminates the need for secondary installation of inserts, reducing costs compared to installing inserts into plastic parts during post-molding .
Why should we use insert molding?
Inserts are often metal parts and are used to enhance the mechanical properties of plastic parts. The most important reasons to use insert injection molding is can greatly save production savings,insert molding eliminates the need for secondary installation of inserts, reducing costs compared to installing inserts into plastic parts during post-molding .Meanwhile, the other benefit of insert molding is that it is structurally more stable than when inserted after molding.
What are the advantages of using insert molding over traditional injection molding?
A typical application of insert molding is the inclusion of one or more threaded metal inserts in a plastic part when it is intended to mate with another part in an assembly. Plastic alone may not have enough mechanical properties to withstand the forces required to hold the two parts together. For example, threads in plastic parts can wear out with repeated use, causing damage to the part. Metal inserts help enhance the performance of plastics and ensure reliable fastening when parts are reused. This combination of plastic and metal can take advantage of the light weight of plastic and the strength of metal.
What are the main design guidelines to follow when designing an insert molding part?
As with any molded part, typical design guidelines for formability apply to insert molded parts, such as increasing the draft to help the part release from the plastic mold and maintain a consistent wall thickness. In addition, there are some unique factors to consider when designing parts for insert molding. For example, the design of undercut features can help improve the retention strength of the insert within the molded part. Since the insert must be placed in the plastic mold, it is also important to ensure that the insert is in an accessible area of the plastic mold. Making sure the insert is not too deep into the part and securing it in the plastic mold during the molding process will also help ensure a successful outcome.
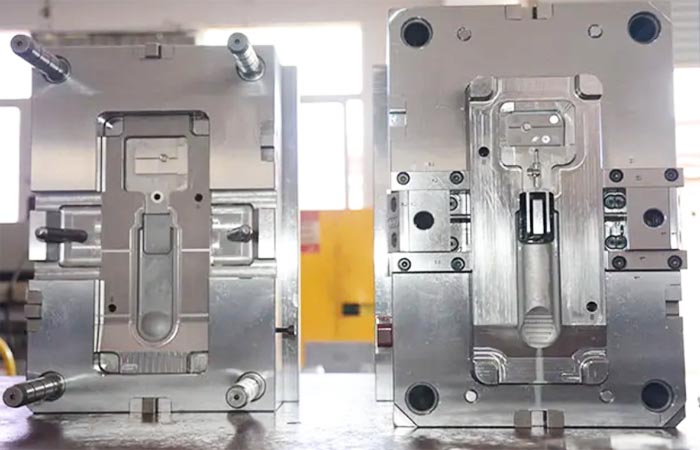
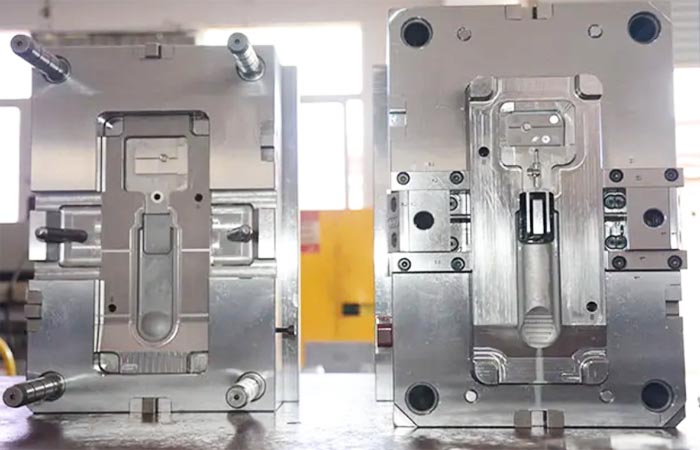
Processing method of metal insert molding
Metal insert molding refers to a molding method in which pre-prepared inserts of different materials are loaded into the mold, resin is injected, and the molten material is bonded and solidified with the inserts to form an integrated injection molded product. At present, many domestic injection molding factories are still lacking in metal inserts.
Metal insert molding is relatively simple, but the resulting molding shrinkage is also relatively non-uniform. Before the injection molding of the product, the limit experiment of the shape and dimensional accuracy of important parts should be done. During the injection molding process, the metal insert is prone to deformation and displacement, so the design should fully consider the mold structure and the mold shape that is easy to maintain the metal insert.
For products where the shape of metal inserts is difficult to change, sufficient experimental preparations should be made in advance. Predictable matters that restrict the structure of the mold, such as the position of the mold gate and the molding cycle, should be solved as much as possible in advance or there are corresponding improvement measures. It should be confirmed whether the metal insert needs to be preheated or dried in order to ensure the quality of the product and the stability of the molding. in order to avoid
Metal inserts and fine pieces of molded products are accumulated in the cavity, and air blowing equipment can be assembled if necessary.
There are many factors that determine the molding rate, productivity and molding cost conditions of metal inserts, such as: the accuracy of metal inserts, the shape of the insert, whether the mold is conducive to insert molding and the shape of the molded product, etc. The effective combination of injection machine, mold and automation device and how to exert its excellent performance in a short time is the key to determine the automatic insert molding system.
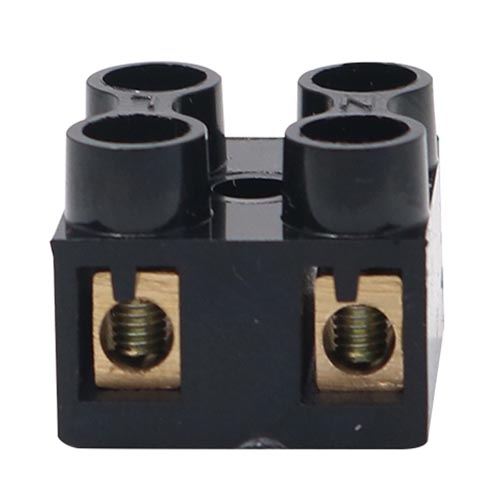
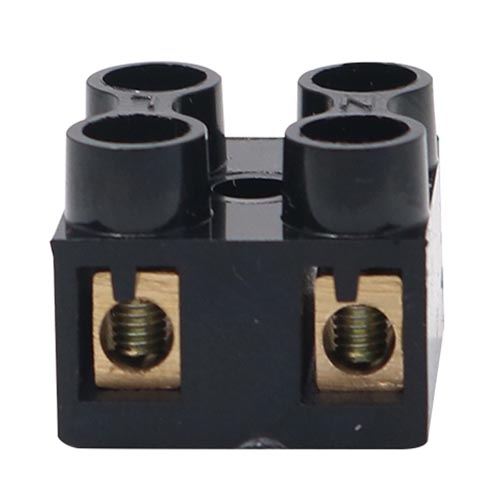
Key points of insert molding
1.Support,no matter what material we use for the insert, we must first ensure that the wall thickness of the plastic part is sufficient to support the insert. Production failed.
2.Temperature,when we produce insert molding molds, we need to ensure that the insert can be safely exposed to the temperatures required to melt the plastic injection molding material and that the insert does not deform.
3.Pressure,It is necessary to consider whether the insert can withstand the corresponding pressure, because the pressure generated in the plastic injection molding process is very large, and the insert needs to be able to withstand enough pressure without cracking or deformation.
Insert molding applications
There have many applications for insert molding, such as auto parts products,industrial equipment parts,medical instruments,couplings parts,threaded fasteners parts,electrical parts ect.
wsmcmold can help you meet with your insert molding needs.
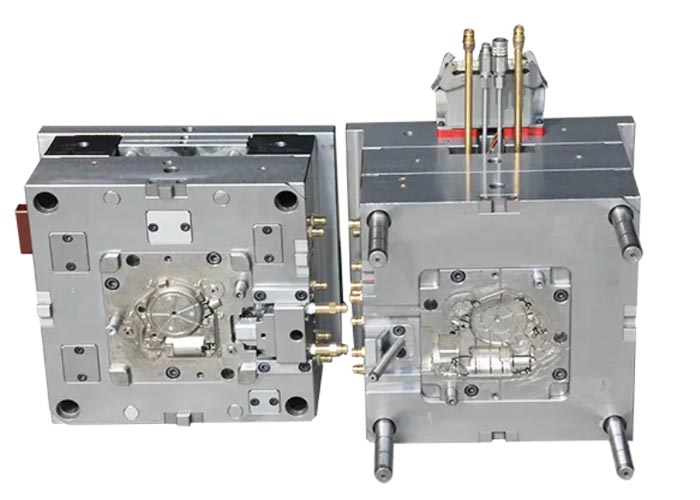
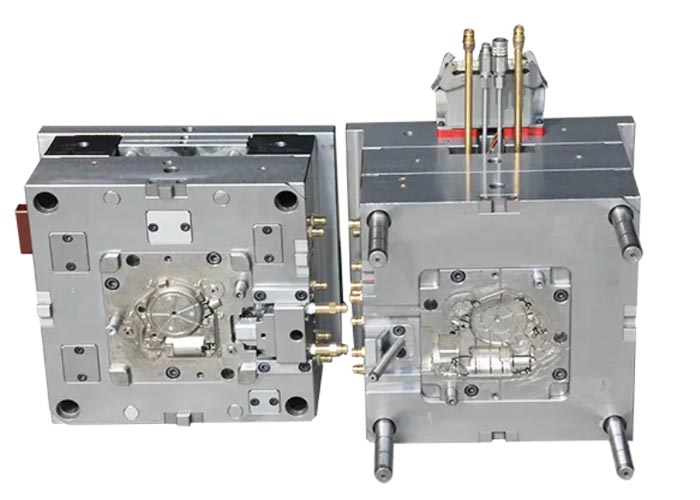
Insert Molding vs Overmolding
Insert injection molding is similar to other molding methods, but there are some differences between each process. Injection molding involves injecting one or more molten plastics into a mold to form a single finished product.
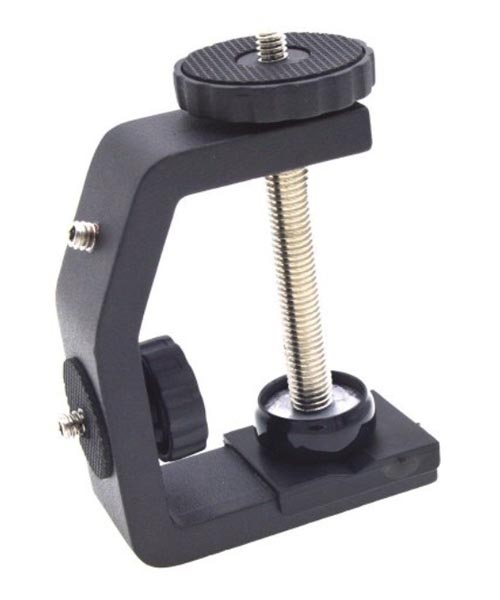
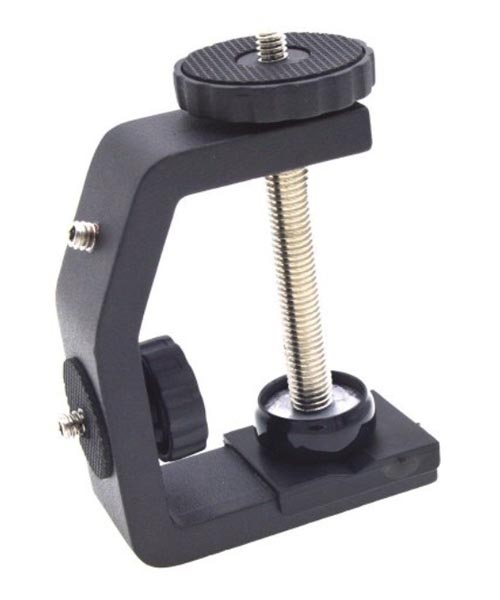
Inserts for plastic insert molding are usually made of brass, steel or stainless steel and have a threaded surface to provide better adhesion to the plastic. Injection-molded inserts are placed in the mold either manually or by machine with the mold in a vertical position.
This position allows gravity to hold the insert in place when the mold is closed. It helps hold the insert in place as the molten plastic slowly pours into the mold.
Insert molding is just one of the many professional plastic injection molding services provided by Mingyang Yutong Injection Mold Factory. Using a highly advanced vertical injection molding machine, our insert molding process enables tight tolerance management to ensure plastic parts are properly molded.
Overmolding is the process of injecting a layer of plastic onto another sheet of plastic of a different material. For example, the shell products of portable drilling rigs are overmolded,the main body of housing is injection molding first, then the softer grips and handles are overmolded onto the main body.
How long does insert molding mould last?
In general,our injection molds will last well over 100,000 shots. Moreover, wsmcmold offers a lifetime warranty for any injection molds which you purechased from us.
How to work with us for insert molding?
1. Send your drawings to get your mold and part quote.
2. List your requirements for inserts molding, and our project manager will contact you.
3. After order confirmation, wsmcmold starts the mold and part order process.
4. Tooling design review by wsmcmold engineers.
5. when you approval the design, wsmcmold begins building your injection mold.
6. Client comfirm samples for approval,then part production begins.