Plastic & Composites Mold 3D Design
Product Design + Mass Production
From design to finished product, one-stop processing, full control
Mold design refers to the personnel engaged in the digital design of enterprise molds, including cavity molds and compression molds, on the basis of traditional mold design, making full use of digital design tools, improving mold design quality, and shortening mold design cycles. In short, it is to make a model before the product is produced, and the mold designer is the one who designs the model.
A mold is an industrial product that forms a material in a specific structural form through a certain method, and is also a production tool that can batch produce industrial product parts with certain shape and size requirements. From airplanes and automobiles to small cups and nails, almost all industrial products must be formed by molds. The high-precision, high-consistency, and high-productivity of parts produced with molds is unmatched by any other processing method. To a large extent, the mold determines the quality, efficiency and new product development capability of the product. Therefore, the mold has the honorary title of “the mother of industry”.
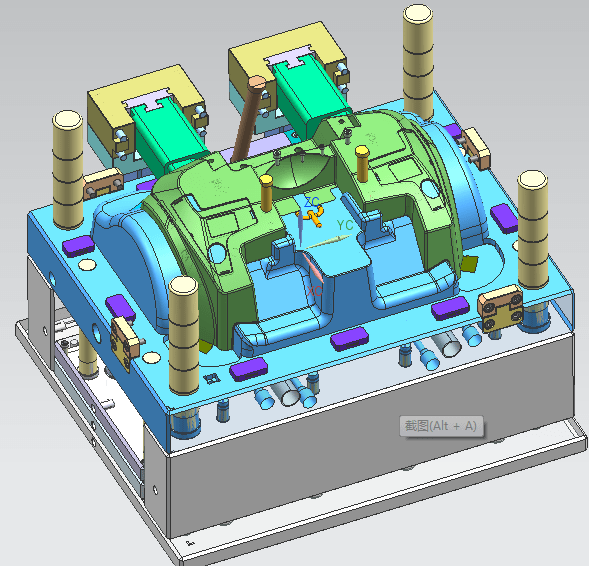
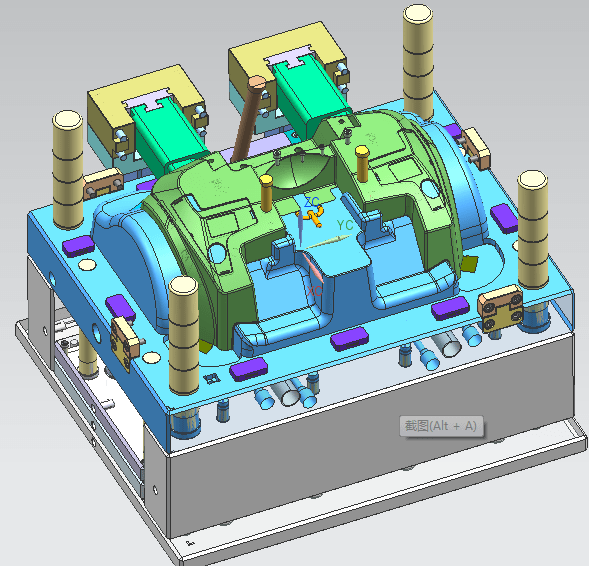
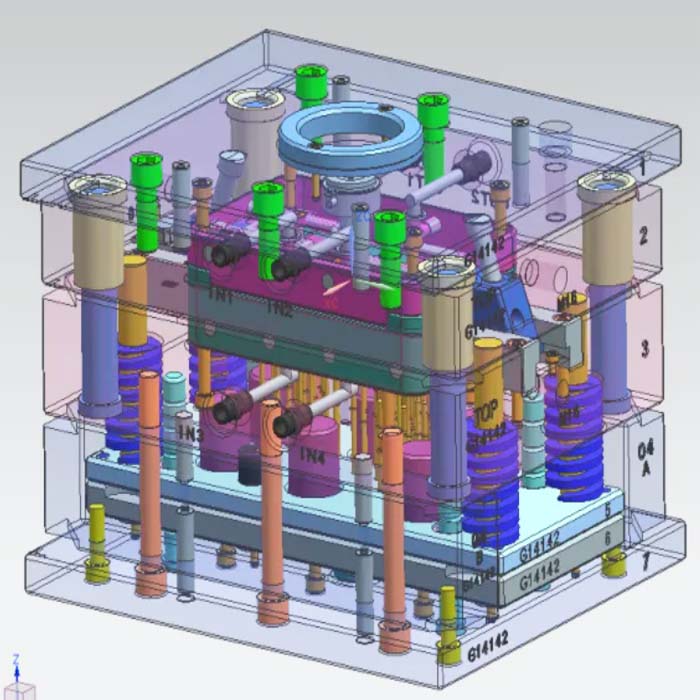
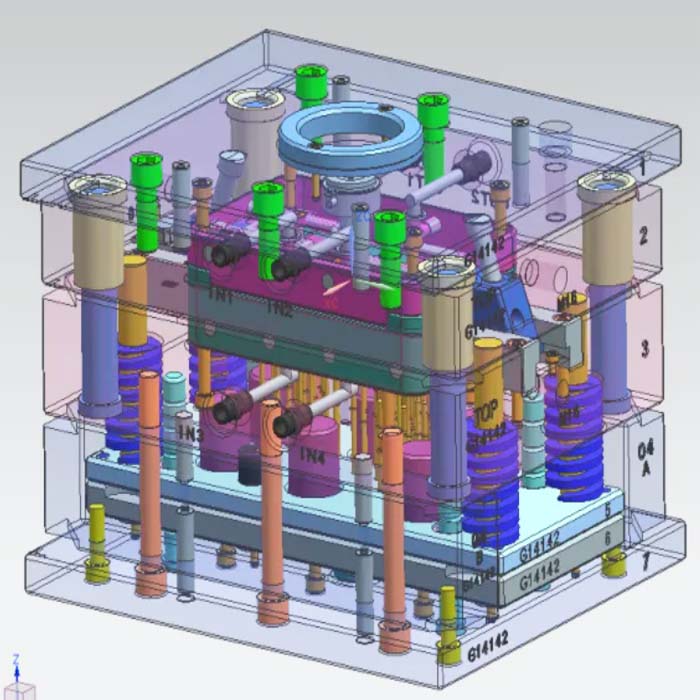
100% customer word-of-mouth trust, exclusive mold custom design
No matter whether you have finished CAD drawings or just an idea or concept, WS can start working with you on your project. We can turn your concept into 3D model design in time.
We support all design stages of product development, from concept to 3D drawings or according to customer samples. We work with our customers to understand the characteristics and production requirements of the desired product, and we make full use of our best knowledge and skills to turn our customers’ ideas into high-quality products.
We have a complete CAD/CAE/CAM system and experienced design engineers, the following are our commonly used design software:
– Pro/Engineer / SolidWorks / Unigraphics (3D Modeling)
– AutoCAD (2D Modeling)
– CATIA (3D Modeling)
– MasterCAM (CNC Programming)
– MoldFlow Mold Advisor (Plastic flow/deform simulation)
We believe that mold design and construction is a critical and important step in mold manufacturing. In order to ensure high-quality plastic parts production, we repeatedly analyze and determine gates, runners, and cooling systems to ensure that the best solution is used. At the same time, we pay more attention to details, such as mold steel, mold base, mold accessories, plastic raw material selection, etc., to ensure the high quality of our molds.
What are the steps in mold design?
1. Analyze the feasibility of designing mold products to ensure the correctness of each product drawing before mold design. On the other hand, we can familiarize ourselves with the importance of the various components throughout the chassis to determine critical dimensions.
2. The work to be done after product analysis, analyze what kind of mold structure the product adopts, and sort the products.
3. Prepare materials, prepare materials according to the product development drawing, and determine the size of the template in the drawing, including each fixed plate, unloading plate, convex and concave mold, inserts, etc., pay attention to preparing materials directly in the product development drawing, which is very useful for drawing mold drawings. big benefit.
4. After the material preparation is completed, you can fully enter the drawing of the mold drawing, make a new copy in the material preparation drawing, and draw each part. In addition, in the process of drawing the mold map, it should be noted that each production, such as fitter marking, wire cutting, etc. There are complete layers for different machining processes, which is a great benefit for wire cutting and drawing management.
5. Proofread mold drawings, set accessories, make different layers for each different template, analyze mold settings with the same benchmark, such as guide post holes, and set the product development diagram of each process into the setting diagram, To ensure that the hole positions of each template are consistent, and whether the clearance between the upper and lower molds at the bending position is correct.
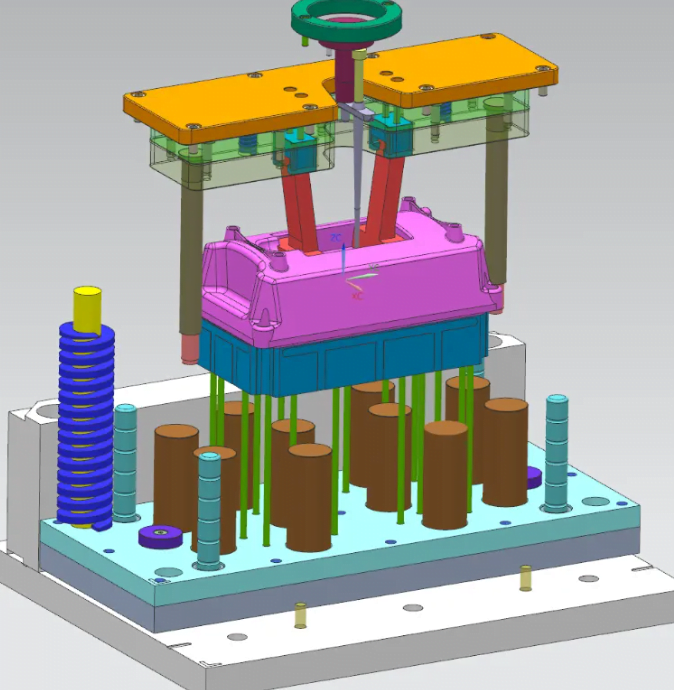
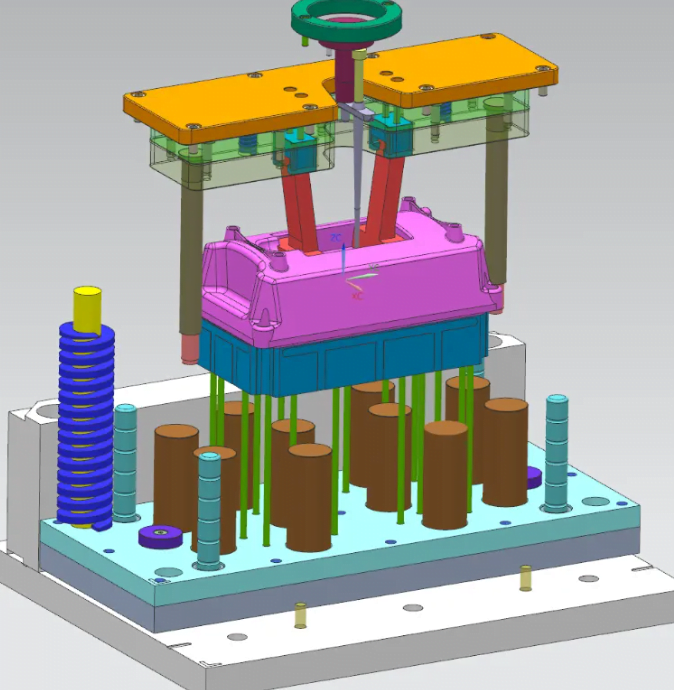
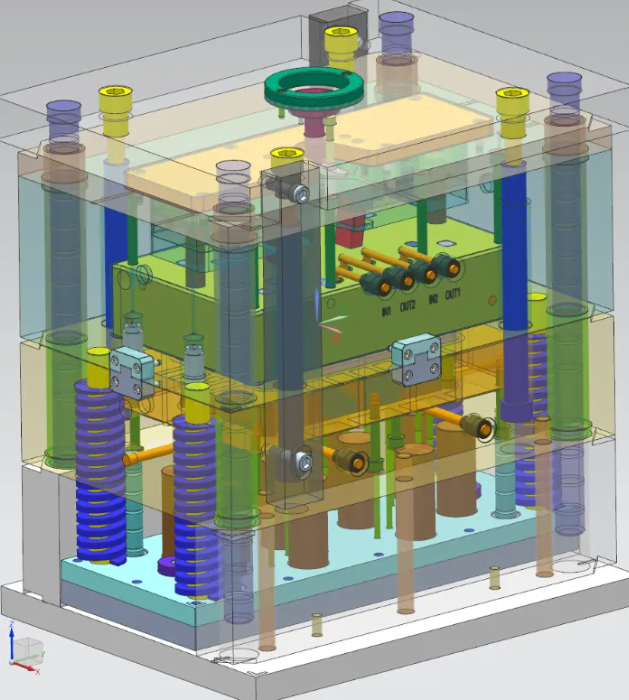
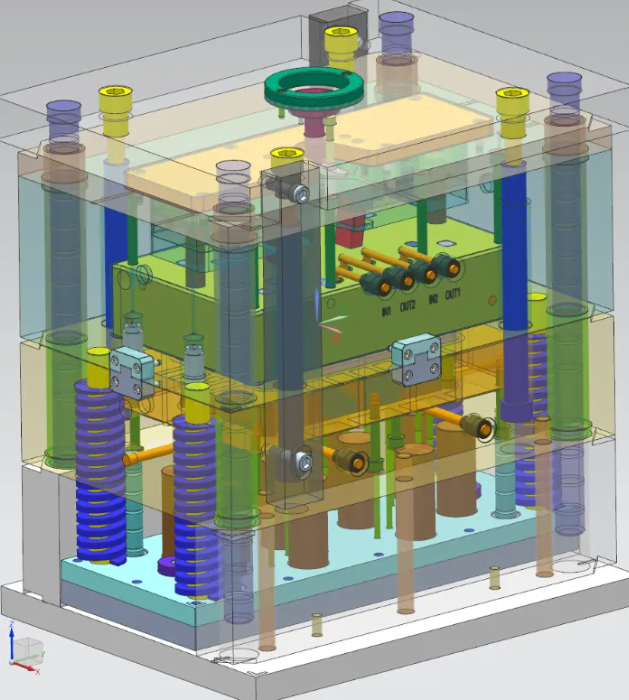
Mold design is mainly for machinery, mold, automobile, aviation, medicine and other industries, and can be engaged in mold design and manufacturing, product structure design and development, equipment debugging and management, numerical control operation and programming, production technology management and other related technical work.