Professional Molds Manufacturer
Mainly engaged in compression moulds, military product moulds, daily necessities moulds, auto parts moulds, medical supplies moulds, home appliance moulds
WS is mold making professional manufacturer, specializing in the production of composite material molding molds and plastic injection molds, efficient injection molding production, and large-scale auto parts mold manufacturing, integrating design optimization, mold processing, and injection molding production.
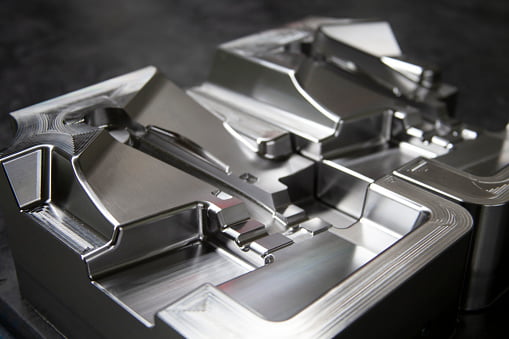
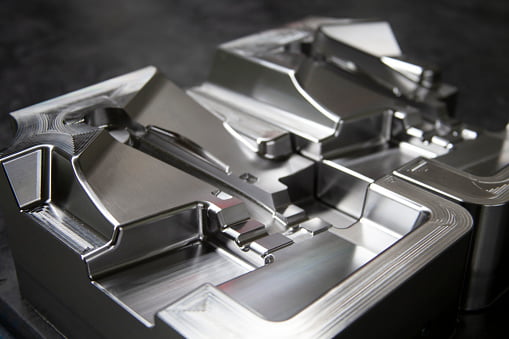
Mold manufacturing process
In general, the process of mold design and manufacturing is roughly divided into the following four steps:
1. Design the mold shape according to the work requirements;
2. Select the mold material and its heating treatment according to the situation, and carry out certain processing;
3. Manufacture the main parts of the mold;
4. Final inspection of the mold.
Molds are widely used in life, and there are many kinds of them. Although it is only a model, many products are produced according to molds, and the role of molds is becoming more and more important.
The mold design is not made out of thin air, but is designed according to certain requirements. Whether it is material, shape, size, and smoothness, it must be completed according to the requirements.
In selecting the material of the mold: the customer’s usage needs and manufacturing costs are mainly considered.
In terms of use requirements: general users will focus on high hardness and wear resistance, which is closely related to heat treatment. If the heat treatment is not done well, the hardness requirements will not be met. If the brittleness is too large during the heating process, there are also It may cause the mold to explode and rupture when heated, so the heat treatment process is also critical.
In terms of manufacturing cost: This kind of fine processing and manufacturing cost also occupies a large proportion. The selection of materials must pay attention to the heating performance to avoid wasting materials and increasing the manufacturing cost.
The main parts of the mold are manufactured:
First of all, pay attention to the grinding of the surface and interior of the mold;
Secondly, when processing the mold, pay attention to the process of wire cutting, because the diameter of the wire is relatively small and the difficulty is relatively high, so special attention should be paid to it;
Finally, when discharging and heating, you should pay attention to avoid the heat generated by the spark when the electrical appliance is working to hurt your eyes.
There are precautions in mold making and processing
1. Don’t focus on product design and ignore mold manufacturing. When developing products or trial production of new products, some users often only focus on product research and development in the initial stage, ignoring communication with mold manufacturing units. After the product design plan is initially determined, contacting the mold manufacturer in advance has two advantages:
(1) It can ensure that the designed product has a good forming process, and the finalized design will not be modified because the parts are difficult to process.
(2) The mold maker can make design preparations in advance to prevent ill-consideration in a hurry and affect the construction period.
In short, to make high-quality molds, only the close cooperation between the supply and demand sides can ultimately reduce the cost and shorten the cycle.
2. Don’t just look at the price, but consider the quality, cycle and service in an all-round way. There are many types of molds, which can be roughly divided into ten categories. According to different requirements of parts material, physical and chemical properties, mechanical strength, dimensional accuracy, surface finish, service life, economy, etc., different types of molds are selected for forming.
Molds with high precision requirements need to be processed by high-precision CNC machine tools, and mold materials and forming processes have strict requirements, and CAD / CAE / CAM mold technology needs to be used for design and analysis. Due to the special requirements of some parts during molding, the mold also needs to use advanced processes such as hot runner, gas-assisted molding, and nitrogen cylinder.
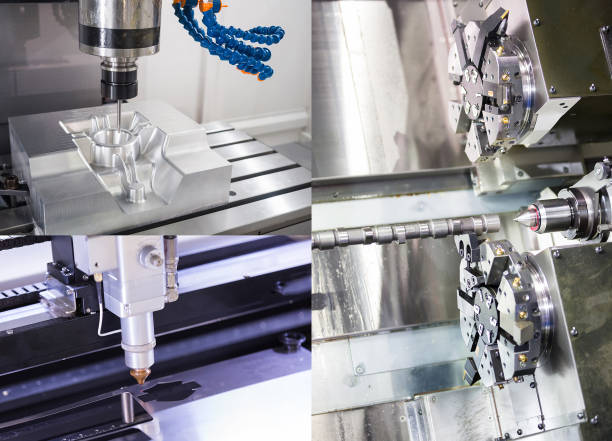
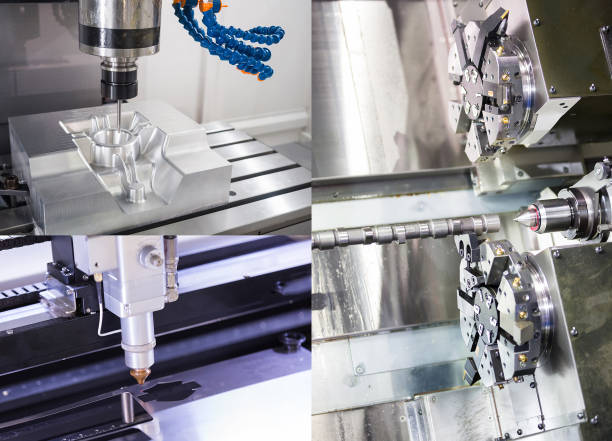
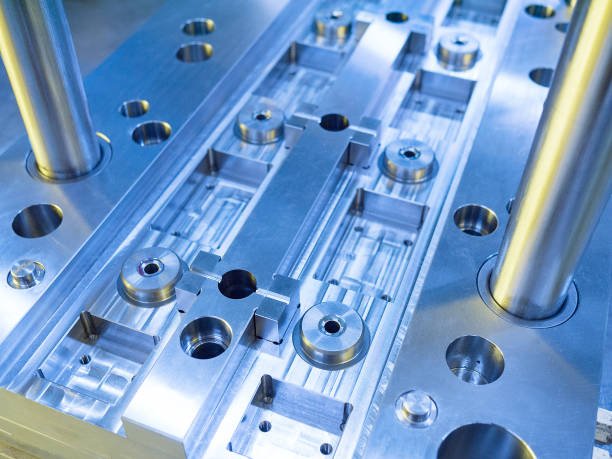
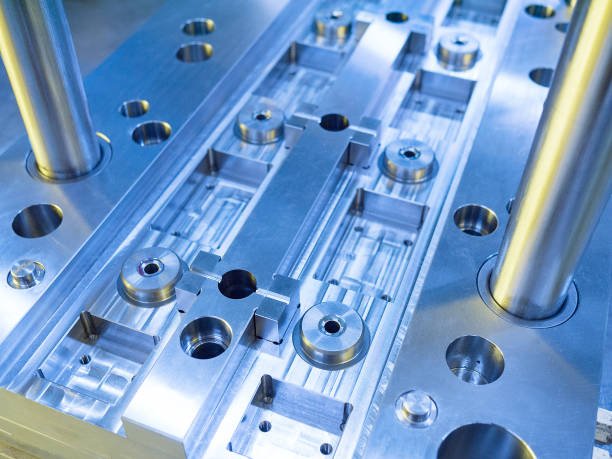
Mold manufacturing requires CNC, EDM, wire cutting machine tools and CNC copying and milling equipment, high-precision grinding machines, high-precision three-coordinate measuring instruments, computer design and related software. For the same set of molds, there is sometimes a big gap between the quotations of different manufacturers. You should not pay more than the value of the mold, nor less than the cost of the mold. Mold manufacturers, like you, want to make reasonable profits in their business. Ordering a set of molds at a much lower price can be the start of trouble. Users must start from their own requirements and comprehensively measure.
3. Avoid multi-head cooperation, try to make molds and product processing in one package. With qualified molds (qualified test pieces), it may not be possible to produce qualified products in batches. This is mainly related to the selection of the machine tool for processing the parts, the forming process (forming temperature, forming time, etc.) and the technical quality of the operator. With a good mold, there is also a good forming process, preferably one-stop cooperation.