Military Bulletproof Products Mold
Human body protection bulletproof helmet and plate mold expert
Dedicated solution provider
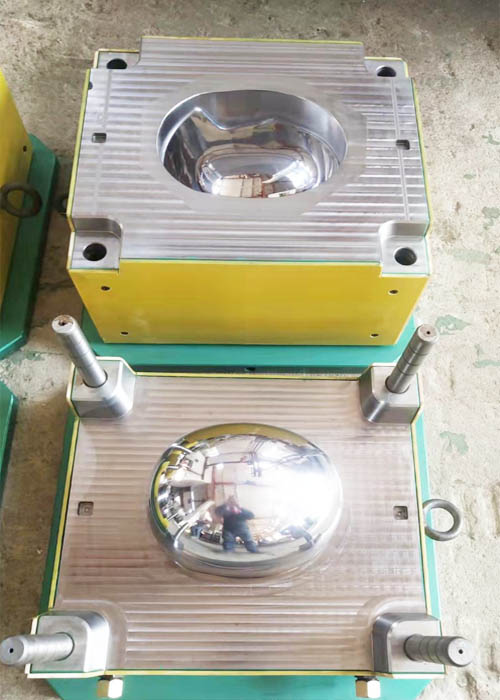
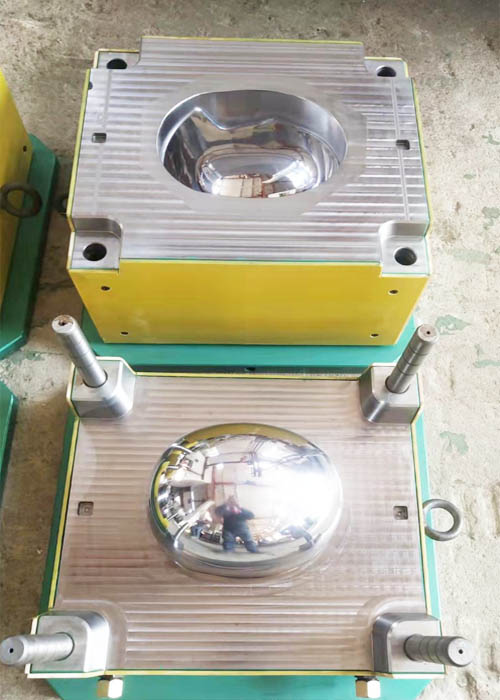
Overview of bulletproof helmets & Molds
Bulletproof helmets are an indispensable protective equipment in the military, security agencies and defense departments. Bulletproof helmet molds are an essential tool for the production of bulletproof helmet products.
The bulletproof helmet is a high-strength tactical helmet made of special materials Kevlar(Aramid), PE(UHMWPE) and steel that can defend against bullet attacks to a certain extent. Among them, aramid and PE are new high-tech synthetic fibers developed in the 1960s and 1980s. Compared with traditional bulletproof steel, they have the advantages of light weight and high strength, so they have been widely used in the production of bulletproof helmets. Aramid and PE helmets under the unified protection level are much lighter in weight than steel helmets, but they are also relatively expensive. In addition, limited by the characteristics of the material itself, aramid and PE helmets also have certain requirements for preservation. For example, aramid helmets should avoid prolonged exposure to sunlight and contact with water, etc.; while PE helmets should avoid contact with high-temperature objects, etc.
WS focuses on the development and production of bulletproof product moulds, and can provide various types and specifications of bulletproof helmet molds, bulletproof body armor plate molds, bulletproof shield molds and related military product molding production.
Types and structures of bulletproof helmet moulds
WS has rich experience in producing FAST ballistic helmet mould, MICH/ACH bulletproof ballistic helmet mould and PASGT ballistic helmet mould.
At present, bulletproof helmets are mainly divided into three types: FAST helmets, MICH helmets and PASGT helmets. Different helmets will vary in structure and functional design, and some of the required gear can usually be worn through the mounting rails. For example, the NIJ IIIA FAST, MICH and PASGT bulletproof helmets produced adopt a new suspension design, the inner lining is molded widow memory foam to make wearing more comfortable, and the helmets are equipped with guide rails. Equipped with night vision goggles, torches and other equipment technicians for your own needs
According to different usage scenarios, there are various sizes and specifications to choose from, among which the NIJ IIIA FAST helmet has a higher ear cut position, and the MICH helmet has a slightly lower ear cut position.
Both can be used with communication equipment such as ear flags, while the PASGT helmet has no ear cut design and has a larger protective area. Customers can choose the corresponding helmet-shaped design.
What is bulletproof body armor chest plate mould?
It is a tool used to make bulletproof insert plate products. When the police officer encounters the threat of high-power bullets, the bulletproof plate is quickly inserted into the front side of the soft bulletproof vest, which can bulletproof the vital organs of the wearer’s torso. Enhance protection.
We specialize in the production of various types of Bulletproof Ballistic Body Armor Plate Mould, which are generally used with various tactical bulletproof vests.Moreover,it is suitable for all kinds of body armor and tactical vests.
Bulletproof plate is an industrial product made of silicon carbide ceramics and used for bulletproof armor.
Silicon carbide ceramics are widely used in bulletproof armor due to their high hardness, low specific gravity, good ballistic performance and low price, such as the protection of vehicles and ships, as well as the protection of civilian safes and cash transport vehicles. The ballistic performance of silicon carbide ceramics is better than that of alumina ceramics, which is about 70-80% of that of boron carbide ceramics, but due to its low price, it is especially suitable for occasions where the dosage is large and the protective armor cannot be too thick or heavy.
The bulletproof plate also includes a silicon carbide bulletproof plate and a composite material bulletproof plate.
WS is ballistic insert mold manufacturer, professional research, development and production of protective compression plate moulds. we are committed to providing customers with professional bulletproof chest plate molds solutions, a leading manufacturer of bulletproof insert molds.
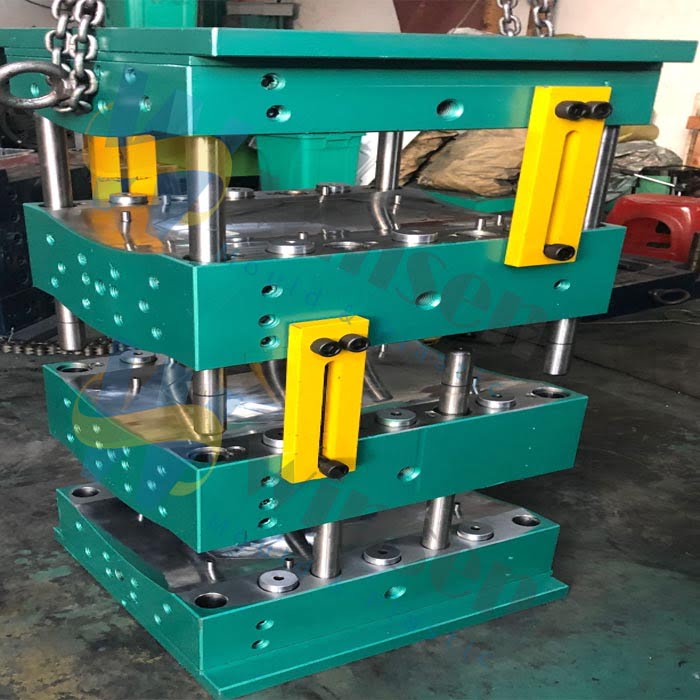
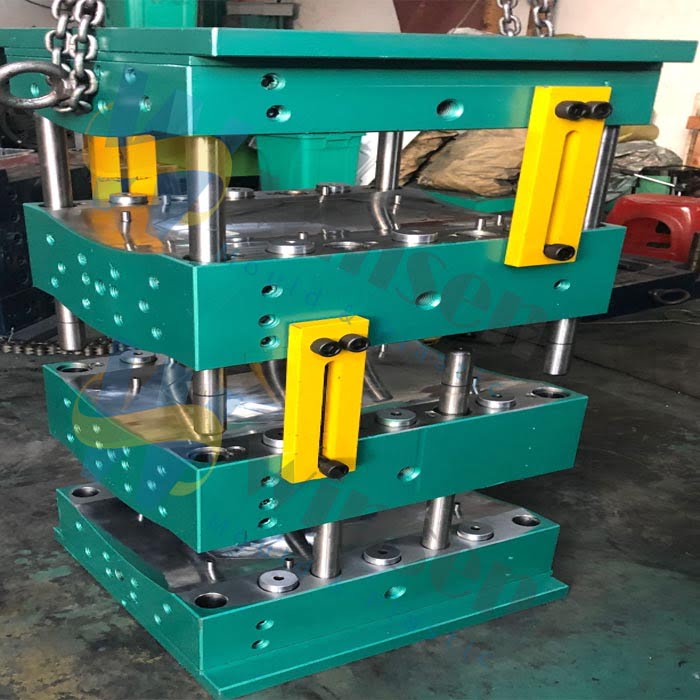
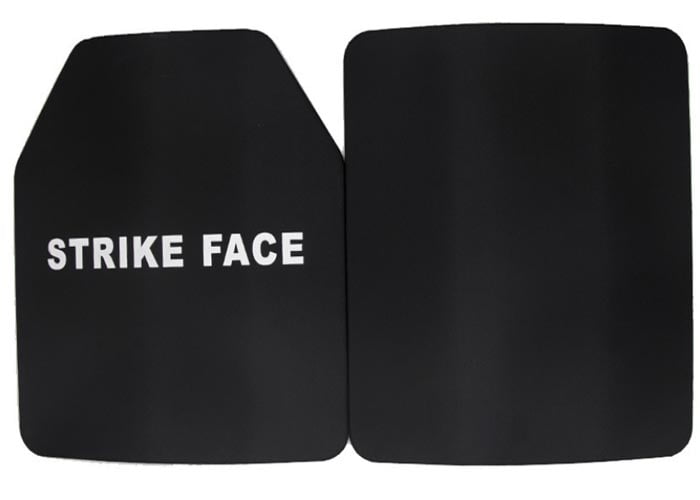
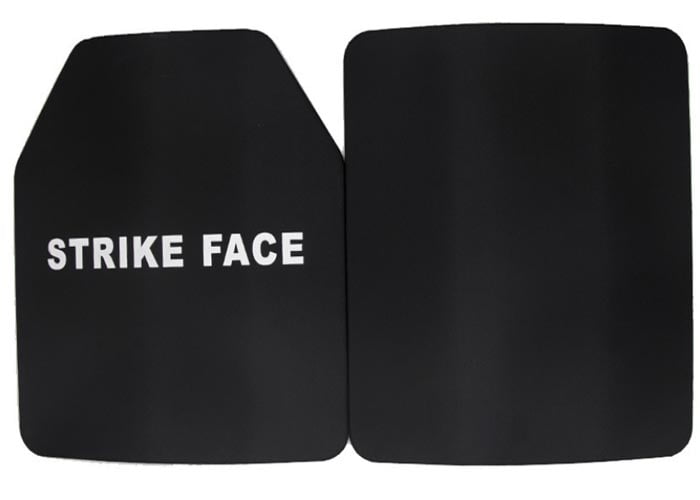
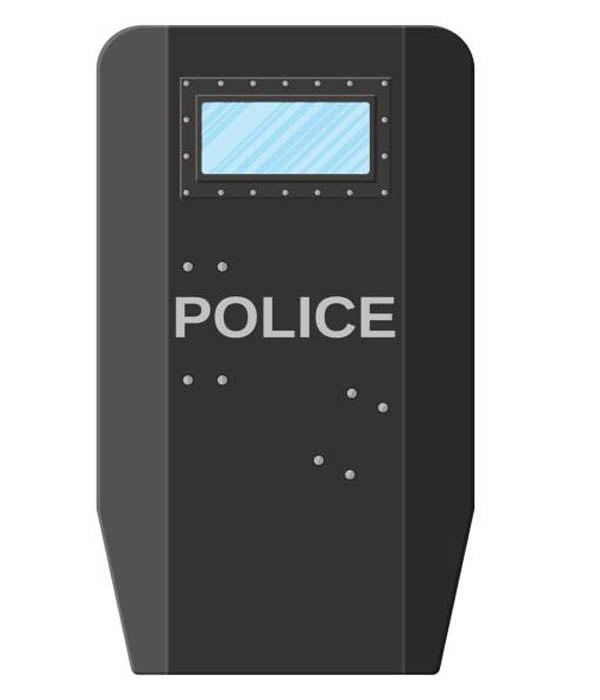
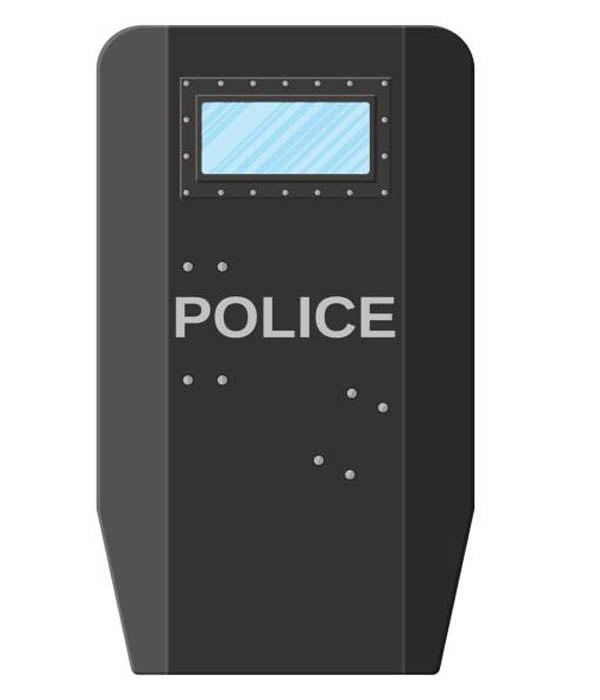
Introduction of bulletproof shield mold and bulletproof shield
As a commonly used and necessary police protective device, bulletproof shields are mainly used to protect people’s bodies from being penetrated by bullets or fragments and be injured, and play a role in protecting human life. Then, the bulletproof shield mold is a necessary tool for the production of bulletproof shields, so the industry of bulletproof shield molds came into being and has developed rapidly.
The hand-held protective shield is a commonly used equipment. The new protective shield is made of dyneema (Dyneema) UD ultra-strong polyethylene material of the Netherlands DSM (DSM) company, KEVLAR (Kevlar) Fang of the American DuPont (DuPont) company. Fiber materials and other super-strength fiber materials and high-strength flame-retardant glass fiber reinforced plastics are pressed by a special process. The products are light and flexible, with good comprehensive protection performance and high protection level, and have been equipped in large quantities across the country.
Since the emergence of new materials and processes, the manufacturing technology of bulletproof shields has advanced by leaps and bounds, and more and more bulletproof shields are used in China. So far, a variety of bulletproof shields have appeared. The more common domestic ones are: hand-held bulletproof shields, wheeled Bulletproof Shield, “Butterfly” Bulletproof Shield, “Briefcase” Bulletproof Shield, Oversized Bulletproof Shield, Foldable Bulletproof Shield.
What is forming of bulletproof helmet Mould and bulletproof armor plate mould and bulletproof shield mould
Ballistic helmet molds and Ballistic helmet body armor chest plate molds & Ballistic shield molds are compression forming, compression molding is also called hot pressing molds. Its production process is to put plastic fiber material(Aramid/Kevlar/UHMWPE) into the heated’s mold cavity, and then close the core and cavity of mold to pressurize the material to shape as a helmet’s work. In addition to this,products of thermosets, thermoplastics and rubber materials are also processed by compression moulding.
Instructions for compression steps of molded bulletproof products moulds
1. Clean up the mold: Clean up the resin and debris left in the mold that was used last time, and keep the mold clean and smooth.
2. Mold preheating: heat treatment of the mold.
3. Apply mold release agent: Apply a certain amount of mold release agent in the groove of the mold to prevent the molded product and mold from sticking together after preheating.
4. Material preparation: Prepare the raw materials of the carbon fiber that will be made into products, and calculate the material area and the number of sheets of the raw materials.
5. Material stacking: The raw materials are stacked layer by layer, and the stacked materials are pre-pressed to form a dense body with regular shape and certain quality.
6. Enter the mold: Put the stacked raw materials into the mold, and at the same time put the plastic air bag inside, close the mold, put the whole into the mold clamping machine, and apply a certain constant pressure and constant temperature to the internal plastic air bag. Set a constant time for it to cure.
7. Cooling and demoulding: Cool for a period of time for the mold that has been hot-pressed for a period of time, then open the mold and carry out demoulding treatment.
8. Processing and molding: After demoulding, the product needs to be cleaned, scrape off the remaining plastic with a steel brush or copper brush, and blow it with compressed air, and polish the molded product to make the surface smooth and tidy.