What Is Plastic Injection Molding
Plastic injection molds represent the convergence of metallurgy, fluid dynamics, and digital innovation.Plastic injection molding is a manufacturing process where molten plastic is injected into a mold cavity under high pressure. Once the plastic cools and solidifies, the mold opens, and the finished part is ejected. This process is highly repeatable, allowing for mass production of identical plastic components with tight tolerances.
Table of Contents
ToggleEvery day, you interact with dozens of products born from a technological marvel: the plastic injection mold. From your toothbrush to automotive dashboards and life-saving medical devices, injection molds silently shape our world. This comprehensive guide reveals why this manufacturing process dominates global production – and how to leverage it for your projects.
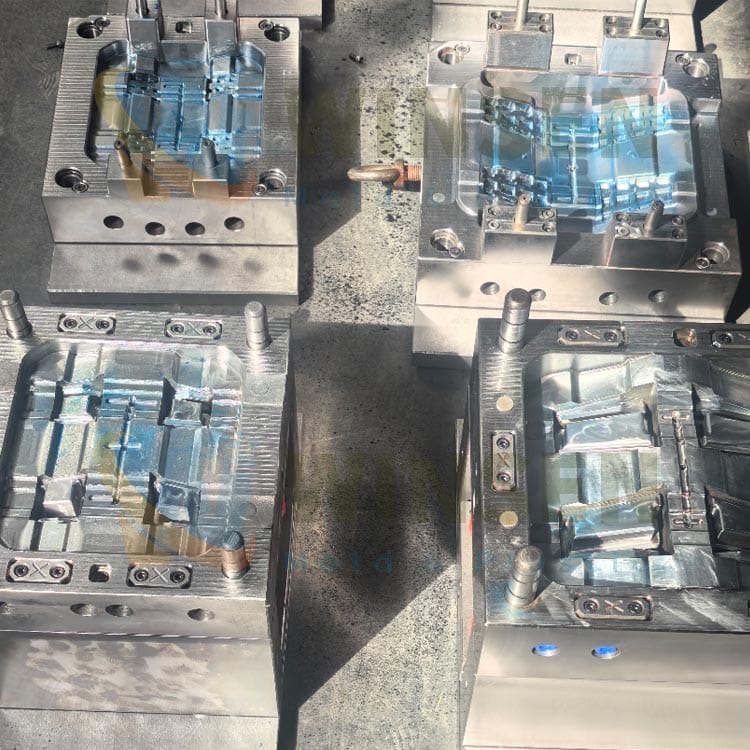
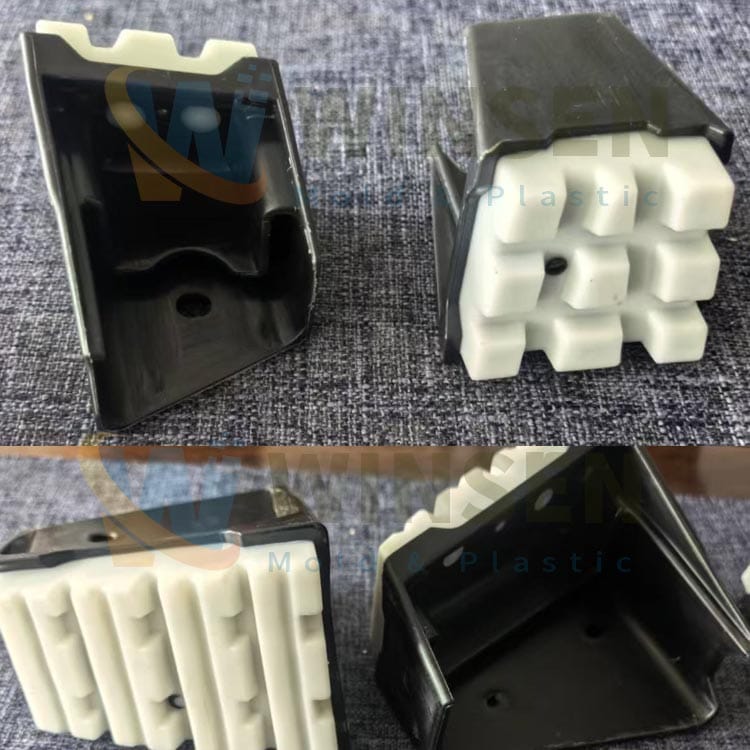
What Makes a Mold
Core & Cavity: Precision-machined steel/aluminum blocks forming the part’s shape
Runner System: Channels guiding molten plastic to cavities
Ejection Pins: Forced removal of cooled parts
Cooling Channels: Critical temperature control system
Venting: Prevents air traps and burn marks
Key Components of a Plastic Injection Mold
Injection Unit – Melts and injects the plastic material into the mold.
Mold (Tool) – A precision-machined metal cavity that shapes the plastic part.
Clamping Unit – Holds the mold halves together during injection and cooling.
Ejection System – Pushes the finished part out of the mold after cooling.
Types of Plastic Injection Molds
Classification by Structure
Two-Plate Molds: Most basic and economical design
Three-Plate Molds: Allow automatic separation of runner system
Hot Runner Molds: Eliminate material waste from runners
Stack Molds: Double production capacity without larger machines
Specialized Mold Types
Overmolding: Combines multiple materials in one cycle
Insert Molding: Encases metal or other components in plastic
Micro Molding: For extremely small, high-precision parts
Gas-Assisted Molding: Creates hollow sections with internal gas channels
How Injection Molding Works
Cycle Breakdown (Typical 15-60 sec)
Clamping: 2,000+ tons force seals mold
Injection: Molten plastic (180-300°C) injected at 1,500+ psi
Packing: Additional material compensates for shrinkage
Cooling: 80% cycle time – determines part warpage
Ejection: Robotic arms remove finished parts
Critical Parameters
- Melt Temperature: ±5°C variance causes defects
- Injection Speed: Impacts surface finish & internal stresses
- Cooling Rate: Governs crystallinity & mechanical properties
- Hold Pressure: Prevents sink marks and voids
Material Matters – Engineering Your Polymer
Top Injection Molding Polymers
ABS: Electronics housings (impact resistance)
Polypropylene (PP): Medical devices (sterilizable)
Polycarbonate (PC): Bulletproof glass (optical clarity)
PEEK: Aerospace (high-temp performance)
TPE/TPU: Ergonomic grips (flexibility)
Material | Characteristics | Typical Applications |
---|---|---|
ABS | Tough, impact-resistant | Automotive parts, toys |
Polypropylene | Chemical resistant, flexible | Food containers, living hinges |
Polycarbonate | Transparent, high impact | Safety glasses, bullet-resistant windows |
Nylon | Wear-resistant, strong | Gears, bearings |
PEEK | High temperature resistance | Aerospace, medical implants |
Material Selection Checklist
☑ End-use temperature ☑ Chemical exposure ☑ Regulatory compliance (FDA, UL94)
☑ Impact resistance ☑ Cost/kg ☑ Recyclability
Design Rules for Mold Success
Avoid Costly Mistakes
Uniform Wall Thickness: (Ideal: 1-3mm) Prevents sink marks
Draft Angles: Minimum 1° per side for clean ejection
Radii Edges: >0.5mm reduces stress concentration
Boss Design: Use ribs to prevent sink around attachments
Gate Location: Impacts weld lines and cosmetic appearance
Tooling Cost Drivers
Since excess material can often be reused, compression molding is more sustainable than other methods.
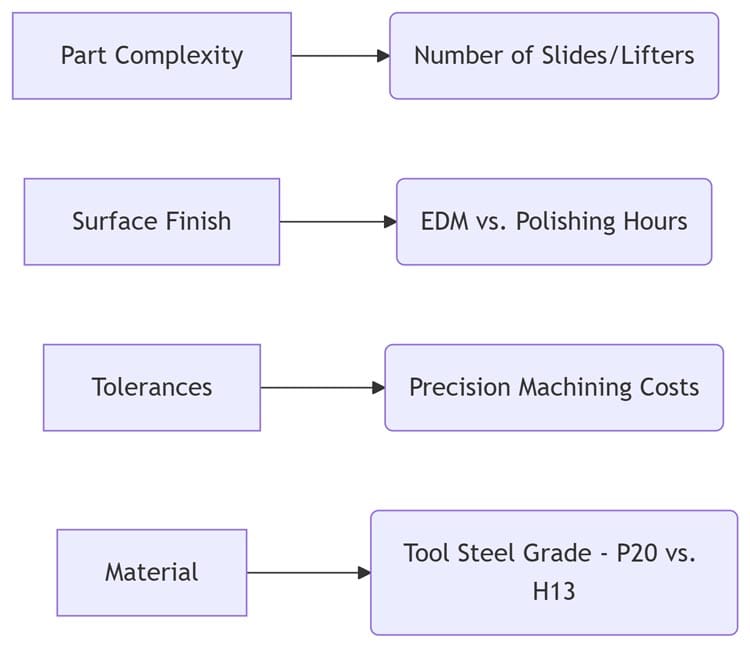
Advanced Applications – Where Molds Make History
Medical:
Micro-molding of <0.1g catheter components
Cleanroom molds with ISO Class 8 certification
Automotive:
72-hour mold changes for just-in-time production
In-mold electronics for dashboard integration
Sustainability Frontiers:
Biodegradable PLA molds for compostable packaging
Gas-assist molding reducing material use by 40%
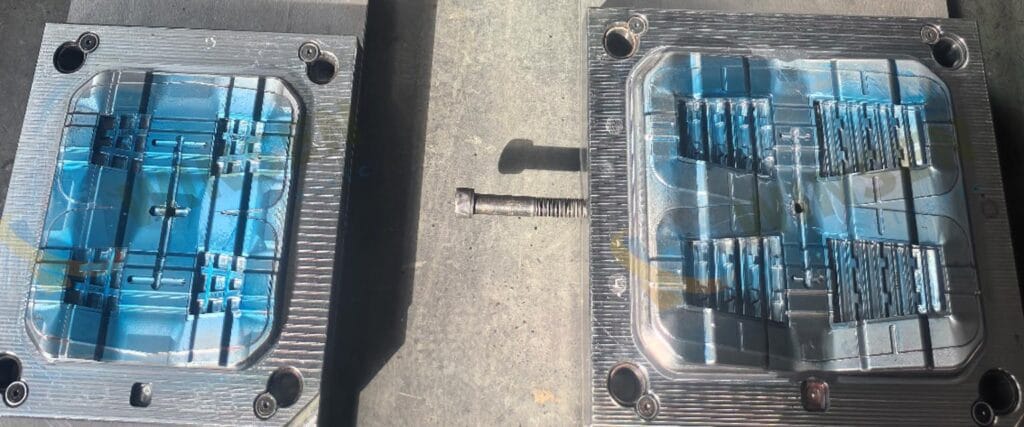
The Future of Mold Technology
Industry 4.0 Integration:
AI-driven predictive maintenance on molds
Real-time pressure/temperature sensors with IIoT
Digital twin simulation for zero-defect launch
Emerging Techniques:
Conformal Cooling: 3D printed molds with organic channels (↓ cycle time 30%)
Mold-in-Color: Eliminating painting process
Hybrid Molds: Combining metal 3D printing and CNC machining
Advantages of Plastic Injection Molding
High Efficiency: Rapid production of thousands of identical parts
Design Flexibility: Complex geometries achievable
Material Variety: Wide range of compatible plastics
Cost Effectiveness: Low per-part cost at high volumes
Precision and Repeatability: Tight tolerances (±0.005 inches achievable)
Minimal Waste: Excess material can often be reground and reused
More Than Just Tooling – Your Competitive Edge
Plastic injection molds represent the convergence of metallurgy, fluid dynamics, and digital innovation. As additive manufacturing advances, traditional molds evolve rather than disappear – becoming smarter, faster, and more sustainable. Whether you’re developing a medical device or consumer product, mastering mold design principles delivers:
✓ 10-30% material cost savings
✓ 50%+ reduction in secondary operations
✓ Production rates of 1,000+ parts/hour
✓ Micron-level precision unattainable by other processes
The mold isn’t just a tool – it’s the physical manifestation of your product’s DNA. Partner with experienced mold engineers early in development to unlock manufacturing excellence.
“Give me the right mold, and I’ll give you a perfect part – every 15 seconds, for a million cycles.”
– Veteran Tooling Engineer, Shenzhen
Looking to develop your injection molded product?
[Contact our design team for a free DFM (Design for Manufacturability) analysis]