Master BMC Molding: 5 Techniques for Superior Composites
In the field of composite materials, a material called BMC (Bulk Molding Compound) is quietly changing the rules of the game in the manufacturing industry. Imagine: a material that can simultaneously achieve the strength of metal, the molding freedom of plastic, and the heat resistance of ceramics – this is the engineering miracle created by BMC bulk molding compound Mold.
Table of Contents
Toggle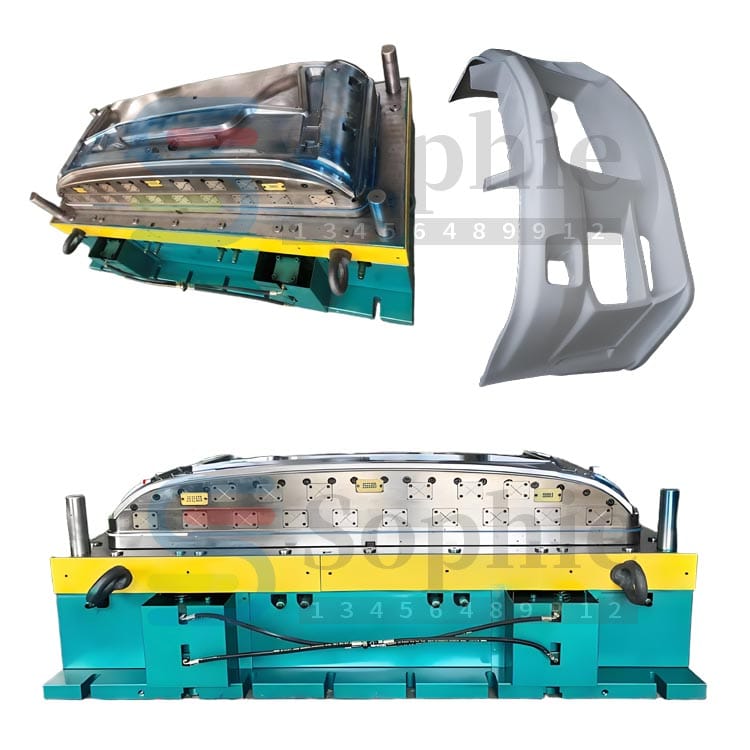
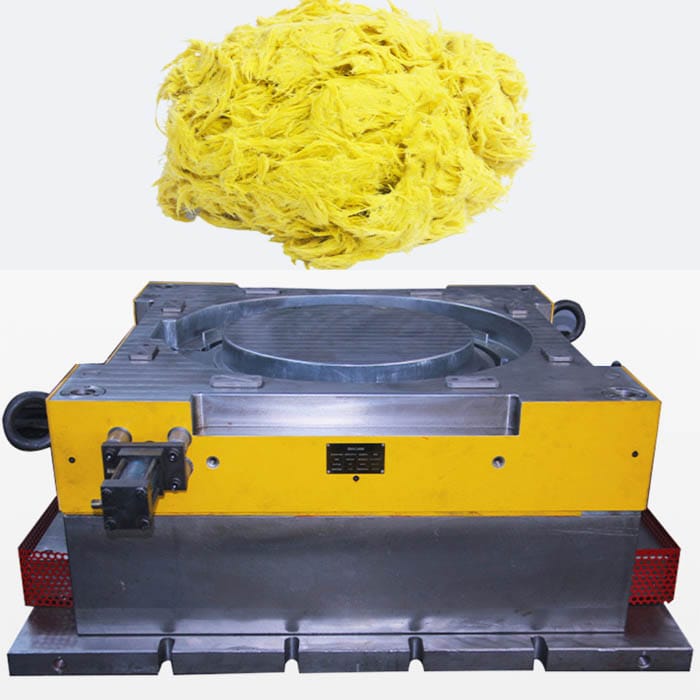
What is BMC? The "universal clay" of the industry
BMC stands for Bulk Molding Compound Mold, which is a bulk prepreg made by mixing unsaturated polyester resin (UP), chopped glass fiber (GF) (usually 15%-25%), calcium carbonate and other fillers (MD) and additives through internal mixing. This material originated in Germany and the United Kingdom in the 1960s, and achieved technological breakthroughs in the United States and Japan in the 1970s and 1980s. It has now become an irreplaceable basic material for high-end manufacturing.
Unlike traditional plastics, BMC is a thermosetting material – it undergoes a permanent curing reaction after heating. Its unique bulk shape is like “engineering putty”, and it can be used to form complex structural parts through molding, injection molding and other processes. It is known as the “universal clay of the industry”
Five performance advantages: Why do the world's top manufacturers choose BMC?
Extreme dimensional stability
The shrinkage rate is only 0-0.5% (adjustable to near-zero shrinkage), and the linear expansion coefficient (1.3-3.5×10⁻⁵K⁻¹) is close to that of metal aluminum, supporting the design of metal-plastic composite structures.
Strong environmental resistance
Heat resistance: heat deformation temperature 200-280℃, long-term use temperature 130℃;
Aging resistance: Strength retention rate >60% after 10 years of outdoor exposure, indoor life of 15-20 years;
Chemical resistance: Water, ethanol, grease resistant, but ketones/aromatic hydrocarbons must be avoided
Excellent electrical insulation performance
The insulation performance remains unchanged after immersion for 24 hours, and the arc resistance is up to 190 seconds (far exceeding ordinary plastics), which is an ideal choice for circuit breaker housings/insulators.
Lightweight and strong
It is more than 40% lighter than aluminum alloy parts, and can bear structural loads exceeding metal by integrated reinforcement rib design.
Surface process freedom
Supports customization of more than 75 colors, compatible with spray/water-based coatings, and achieves Class A surface finish.
Decoding the BMC molding process: the transformation from "putty" to precision parts
Key points of core equipment transformation
- Forced feeding system: Screw/plunger injection molding machines need to be equipped with plunger pressure devices to solve the problem of feeding lumps
- Low-damage screw: speed limit is 20-50r/min, back pressure is 1.4-2.0MPa, to protect glass fiber
- Precise temperature control: the barrel adopts constant temperature water/oil circulation heating, gradient temperature control (nozzle end > hopper end 20-60℃)
Golden range of process parameters
Unlike injection molding, which requires expensive tooling, compression molding is more affordable for large, low-to-medium volume production runs.
Parameter | Optimal Range | Impact |
---|---|---|
Injection Pressure | 80-160 MPa | Overcomes high viscosity and poor flow characteristics |
Injection Speed | 1.8-3.5 m/min | Excessive speed causes fiber orientation issues and venting problems |
Mold Temperature | 135-185°C | Determines curing rate |
Injection Time | 2-20 s | Increases with part complexity |
Curing Time | 10-20 s/mm thickness | Ensures complete curing |
Panoramic view of application scenarios: A crossover king from automobiles to aerospace
Electrical field (largest application market)
- High-voltage components: meter boxes, circuit breaker housings (arc resistance 190 seconds)
- Precision connectors: terminal blocks (dimensional accuracy ±0.1mm)
Automotive lightweight revolution
- Lighting system: headlight reflective surface (high temperature resistance + high reflectivity)
Functional structural parts: gearbox components, valve covers (40% weight reduction vs. metal)
Aerospace breakthrough
Toray develops carbon fiber reinforced BMC for rocket high temperature resistant parts, with a molding cycle of only 10-15 minutes
Emerging growth points
Food utensils: microwave tableware (must comply with FDA styrene-free standards)
Medical equipment: disinfection-resistant instrument housing

Why Top Industries Choose BMC: 5 Superpowers
Property | Performance | Competitive Edge |
---|---|---|
Dimensional Stability | 0.05-0.2% shrinkage | ±0.1mm precision in connectors |
Heat Resistance | 280°C peak HDT | Survives engine bays |
Electrical Insulation | 190 sec arc resistance | Perfect for EV battery housings |
Corrosion Proof | Zero rust vs. metals | 20+ year outdoor lifespan |
Weight Savings | 40% lighter than aluminum | Fuel efficiency booster |
Technology Frontier: Three Evolutionary Directions of BMC 4.0
- Fiber Upgrade: Carbon Fiber BMC (Toray) has a 3-fold increase in tensile strength and is used in aviation structural parts;
- Matrix Innovation: Aerospace-grade thermoplastic BMC (PEEK/PPS-based) has a temperature tolerance of >300°C
- Digital Twin Process: In-mold sensors monitor glass fiber orientation in real time and dynamically adjust injection molding parameters
Conclusion: Master BMC and win in the next decade of manufacturing
BMC is not an ordinary plastic, but an engineering solution that combines design freedom, excellent performance and cost efficiency. With the breakthrough of short-cut carbon fiber reinforced BMC and intelligent molding technology, it is moving from electrical parts to cutting-edge fields such as rocket engine casings.
Industry insight: The key to the successful application of BMC lies in the trinity of “material-process-design”:
- Clarify the requirements for temperature resistance/insulation/food contact in the material selection stage
- Mold design compensates for shrinkage below 0.5%
- Use low-pressure and slow injection molding to protect fiber integrity
In the future, as environmental regulations become stricter, bio-based resin BMC and recyclable thermoplastic BMC will become research and development hotspots, opening a new era of green manufacturing.
This article deeply analyzes the characteristics and processes of BMC materials. Please indicate the source when reprinting. Collect it now to unlock more cutting-edge composite materials technology!