In modern manufacturing, compression molding is a key process that allows rubber and plastic materials to be molded into a variety of complex and precise shapes. This technology is favored for its efficiency, economy, and ability to produce high-strength components. This article “Compression Molding Techniques – A Comprehensive Guide” will take a deep dive into the basic principles of compression molding, how it is done, and its unique advantages over other manufacturing methods. Whether you are new to the industry or an expert looking to optimize your existing production processes, this article will provide you with valuable information and insights. Let’s explore the world of compression molding and learn how it helps modern industry create more durable and precise products
Table of Contents
ToggleCompression Molding Defined
The term “molding” refers to a collection of processes that use molds to shape materials, typically rubber or plastic, into the required parts and products. Manufacturers can choose from various molding techniques to meet different product and production specifications. One such technique is compression molding.
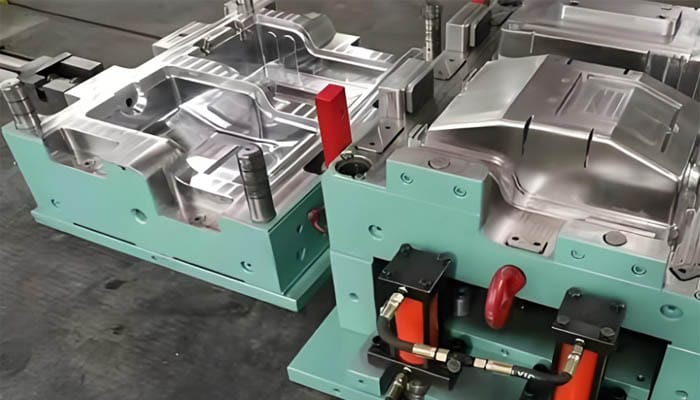
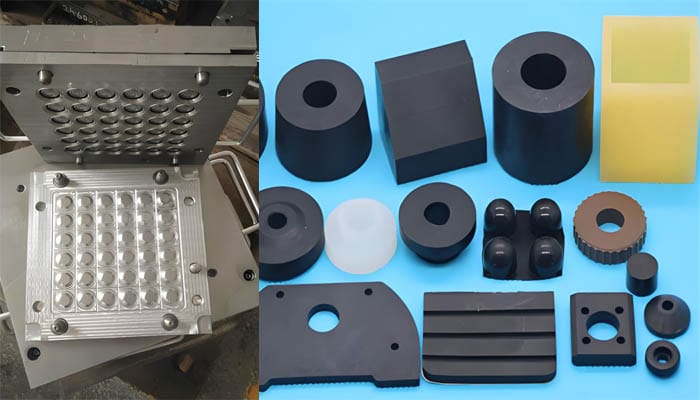
Understanding Compression Molding
Compression molding of rubber or plastic materials is a process where pre-shaped and/or pre-heated raw materials are compressed within a heated mold cavity. The material is subjected to high pressure, causing it to take on the form of the die cavity and, once cooled, to retain that shape. Here, we provide a detailed explanation of the process and its benefits over alternative manufacturing methods.
The Compression Molding Process Explained
While all molding techniques share fundamental principles, they differ in the specific steps used to create molded parts or products. The compression molding process generally involves the following steps:
- Mold Design and Acquisition: The process begins with obtaining a suitable two-part compression mold to produce the desired component.
- Pre-form Creation: The molding material is shaped into a pre-form, which may resemble the final component but is slightly larger to ensure complete filling of the mold cavity.
- Mold Heating: The mold is heated to facilitate the curing of the material, which contains a heat-sensitive catalyst.
- Pre-form Placement: The pre-forms are placed into the heated mold cavity and the mold is closed.
- Heat and Pressure Application: Heat and pressure are applied to the mold and pre-form, causing the material to fill and conform to the mold cavity. Excess material can escape from the mold.
Component - Ejection: Once the component is formed, it is removed from the mold.
- Excess Material Removal: Any excess material (flash) is trimmed from the molded component.
Benefits of Compression Molding
Compression molding offers several advantages over other molding and manufacturing methods:
- Design Flexibility: The process is adaptable, allowing for the production of components in a variety of shapes, sizes, and complexities.
- Strong Components: Components produced through compression molding tend to have minimal residual stress.
- Reduced Waste: Compression molding generates less material waste compared to injection and transfer molding, making it suitable for expensive materials.
- Lower Tooling Costs: The tooling required for compression molding is simpler and less costly than that used in injection or transfer molding.
- Large Part Capability: Since material is loaded directly into the mold cavity, compression molding can produce larger parts, limited only by the press size, pressure capacity, and mold design.
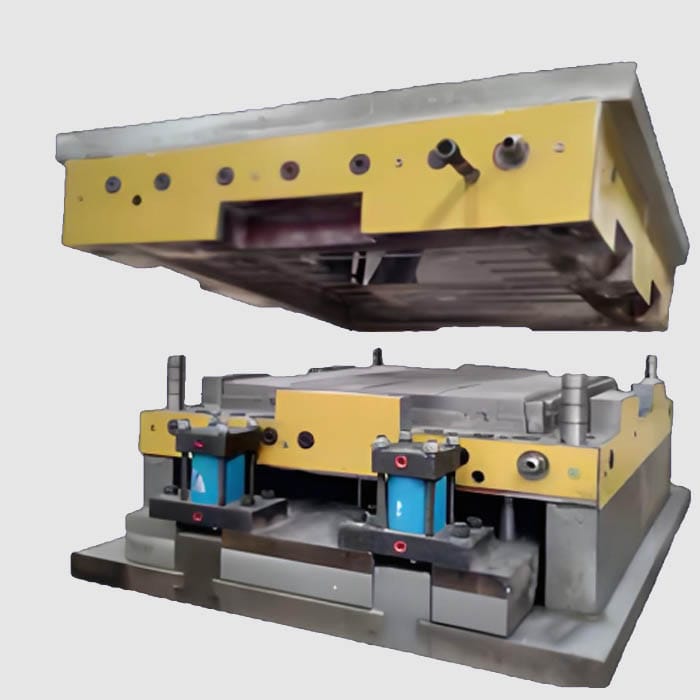
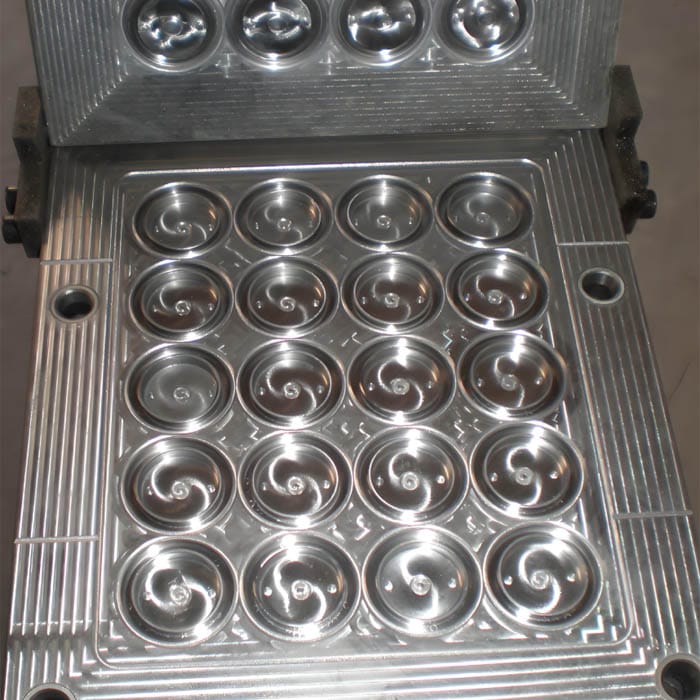
Collaborate with Experts in Compression Molding
For your next compression molding project, consider partnering with WS MOLD. We are a leading contract molding provider with compression molding as one of our core services. We specialize in molding a range of materials, including butyl, EPDM, nitrile, polyisoprene, silicone, and Viton®, into components of various sizes and complexities.
To discover more about our compression molding capabilities, visit our compression molding services page.
For a consultation on your specific molding requirements, reach out to us today.