Export-Ready: Precision Compression Moulds & Thermal Systems
In the heart of industrial manufacturing, compression moulding remains a cornerstone for producing high-strength, complex parts. From automotive composites to aerospace seals, this process delivers unmatched durability. But behind every perfect moulded part lies critical technology: precision compression moulds and specialized heating and cooling equipment. As global demand surges, we’re proud to share insights into this process compression molds and our latest export milestone – with exclusive shipment visuals!
Table of Contents
Toggle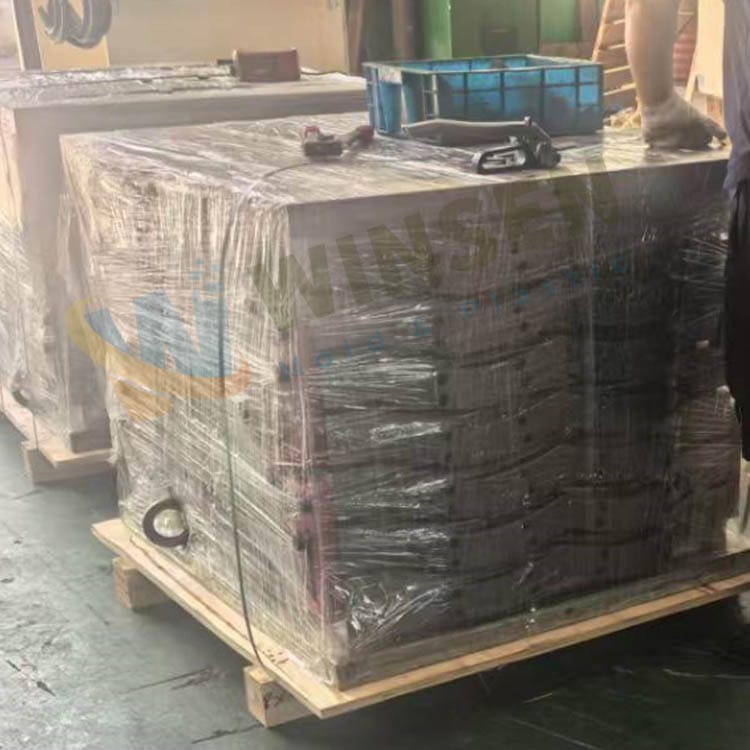
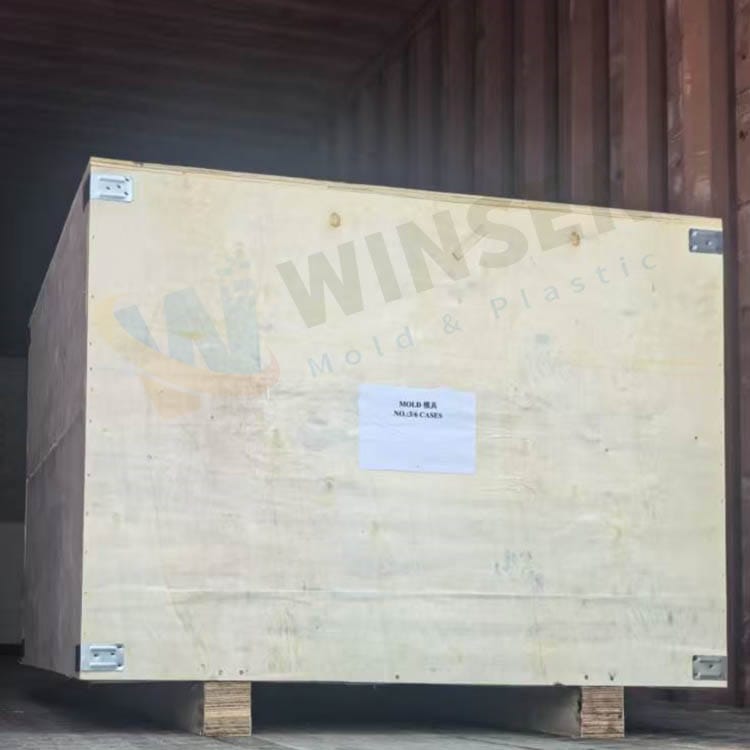
Why Compression Moulding Dominates Heavy-Duty Manufacturing
Unlike injection moulding, compression moulding uses direct pressure to shape materials without high-velocity flows. This makes it ideal for:
Thermosetting plastics (phenolics, epoxy)
Rubber compounds
Key Industries Served:
🚗 Automotive (brake pads, gaskets)
✈️ Aerospace (cowlings, insulation)
🔌 Electrical (switchgear, insulators)
🏭 Industrial (pump housings, conveyor parts)
The Anatomy of a Compression Moulding System
1. The Heart: Compression Moulds
Material: Hardened tool steel (H13, P20) or aluminum for rapid cycling
Design: Custom cavities with vents to avoid air traps
Surface: Polished or textured finishes for part aesthetics
Lifespan: 100,000+ cycles with proper maintenance
*Fun Fact: Our recent export included 4-ton multi-cavity armor plate moulds and shield molds for military bulletproof products!*
2. Heating Systems – The "Ignition" Phase
Precise temperature control ensures uniform curing. Critical equipment includes:
Heating Type | Best For | Temperature Range | Accuracy |
---|---|---|---|
Electric Cartridge | Small moulds | 200-400°C | ±2°C |
Steam/Hot Oil | Large industrial moulds | 150-350°C | ±5°C |
Induction Heating | Ultra-fast cycling | Up to 600°C | ±1°C |
⚠️ Pro Tip: Overheating degrades thermosets – closed-loop PID controllers are non-negotiable!
3. Cooling Systems – The "Lock-In" Phase
Rapid, uniform cooling prevents warping and optimizes cycle times:
Water Channels: Machined into mould plates (most efficient)
Chiller Units: Maintain coolant at 5-25°C
Air Knives: For secondary cooling after ejection
*”A 10% reduction in cooling time can boost output by 1,500+ parts/month in high-volume production.” – Our Engineering Team*
5 Reasons Manufacturers Choose Compression Moulding
Lower Tooling Costs vs. injection moulding (simpler mould designs)
Minimal Residual Stresses from gentle material flow
Massive Part Capability (up to 150 sq. ft. surface area)
Material Versatility – From carbon fiber composites to silicone rubber
Sustainability: Near-zero material loss with flash recycling
Our Global Equipment Export Operations
Today we are currently exporting PE armor plate compression moulds and heating/cooling systems to partners in Ukraine, below are some of our loading goods displays:
Step 1: Laser alignment checks for mould platens
Step 2: 48-hour thermal cycling test on heating units
Step 3: Vibration-proof wooden crating with IP67-rated seals
Step 4: Real-time container monitoring (temperature/humidity)
Exclusive Shipment Snapshots:
(Insert your container-loading photos here with captions)
📸 Image 1: *Custom 800-ton compression press secured for ocean freight*
📸 Image 2: Temperature-controlled cooling units being loaded in Shanghai
📸 Image 3: Laser-etched compression moulds in export-ready packaging
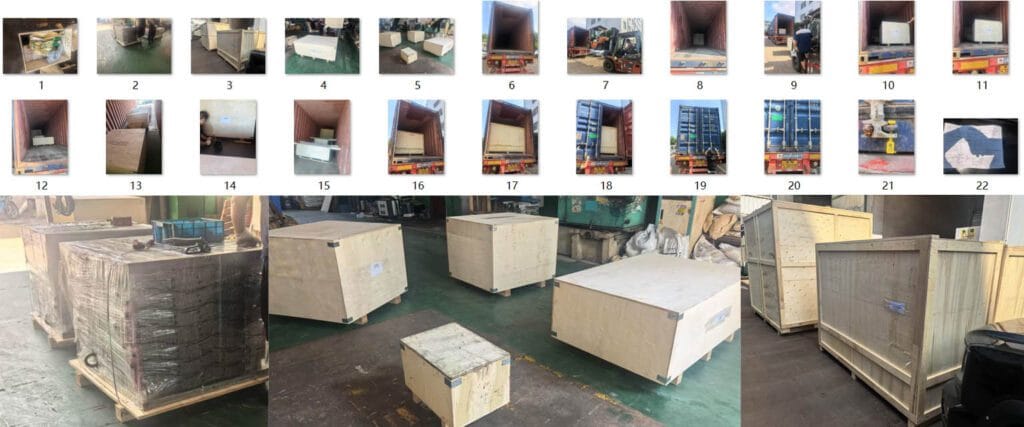
The Future: Smart Compression Moulding 4.0
Emerging tech we’re integrating into next-gen exports:
IoT Sensors: Live monitoring of mould temperature gradients
AI-Optimized Cycles: Machine learning reduces cure time by 15-30%
Hybrid Heating: Induction + cartridge systems for energy savings
Automated Flash Removal: Robotics for post-ejection trimming
Why Partner With Us?
“After importing their compression mould cooling system, our cycle times dropped by 22%.” – Automotive Tier 1 Supplier, Czech Republic
We deliver:
✅ Turnkey Systems: Moulds + heating/cooling + presses
✅ Global Logistics: EXW/FOB/DDP shipping expertise
✅ Onsite Training: Bilingual technical teams
✅ Spare Parts Guarantee: 72-hour emergency dispatch
Conclusion
Compression moulding’s future is bright – and increasingly global. As material science advances and industries demand larger, stronger components, the right compression moulds and heating/cooling equipment become competitive differentiators. We’re honored to supply world-class manufacturers across 18 countries and counting.
Ready to upgrade your compression moulding line?
➡️ Contact us for a free quote for compression molding solution
➡️ Consult our “Compression Moulding Heating Optimization” technology
➡️ Send your project of compression molding for us to customize!